Expertise und Lösungen Automotive
Traceability und Chargenrückverfolgung sind in diesem Umfeld von besonderer Bedeutung. Vertrauen Sie auf unsere Lösungen für Ihre digitale Fertigung.
Ihr Digitalisierungspartner für eine zuverlässige Fertigungssteuerung
Die Welt ist mobil – und unsere Kunden aus der Automotive-Industrie sorgen dafür: Sie produzieren Bremsscheiben, Stoßdämpfer, Scheinwerfer, Tankpumpen, Schläuche, Getriebe, Türgriffe, veredeln Schrauben etc. Und weil Traceability und Chargenrückverfolgung in diesem Umfeld von besonderer Bedeutung sind, vertrauen internationale Top-Anbieter seit Jahren auf unsere Lösungen. Kleine Losgrößen und eine hohe Variantenvielzahl stellen eine von vielen Herausforderungen dar.
Auszug aus unseren Automotive-Kunden
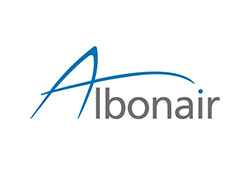
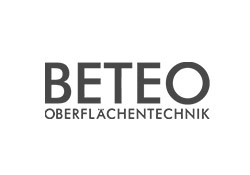
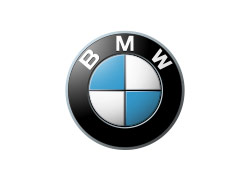
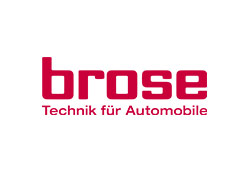
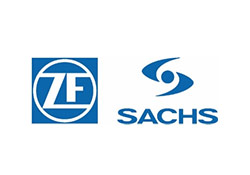

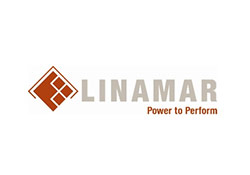
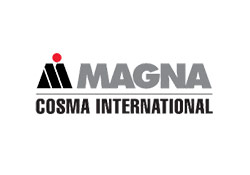
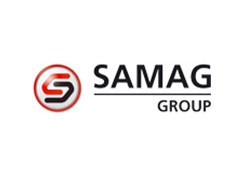
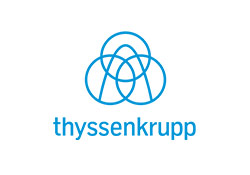
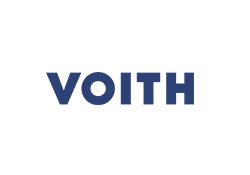
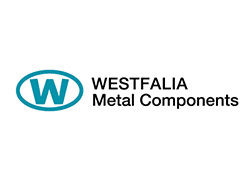
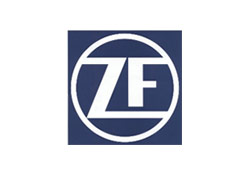
MES FASTEC 4 PRO auf einen Blick – Nutzen, Lösungen, FAQ
Bitte Inhalte erstellen:
Lorem ipsum dolor sit amet, consectetuer adipiscing elit. Aenean commodo ligula eget dolor. Aenean massa. Cum sociis natoque penatibus et magnis dis parturient montes, nascetur ridiculus mus. Donec quam felis, ultricies nec, pellentesque eu, pretium quis, sem
Bitte Inhalte erstellen: Lorem ipsum dolor sit amet, consectetuer adipiscing elit. Aenean commodo ligula eget dolor. Aenean massa. Cum sociis natoque penatibus et magnis dis parturient montes, nascetur ridiculus mus. Donec quam felis, ultricies nec, pellentesque eu, pretium quis, sem.
Komplexere Linien können mit mehreren, parallelen Terminals abgebildet werden. So können in jedem Bereich Eingaben gemacht werden. Eine ideale Lösung, nicht nur bei langen oder unübersichtlichen Linien. Puffer können Linien in zwei Bereiche aufteilen. Störungen in einem Bereich erreichen dadurch verzögert den anderen Bereich. Wenn die Störung dort angekommen ist, wird dort als Information die Dauer der Störung im anderen Bereich angezeigt. So weiß der Mitarbeiter, wann es voraussichtlich weitergeht und er kann zwischenzeitlich andere Aufgaben verrichten.
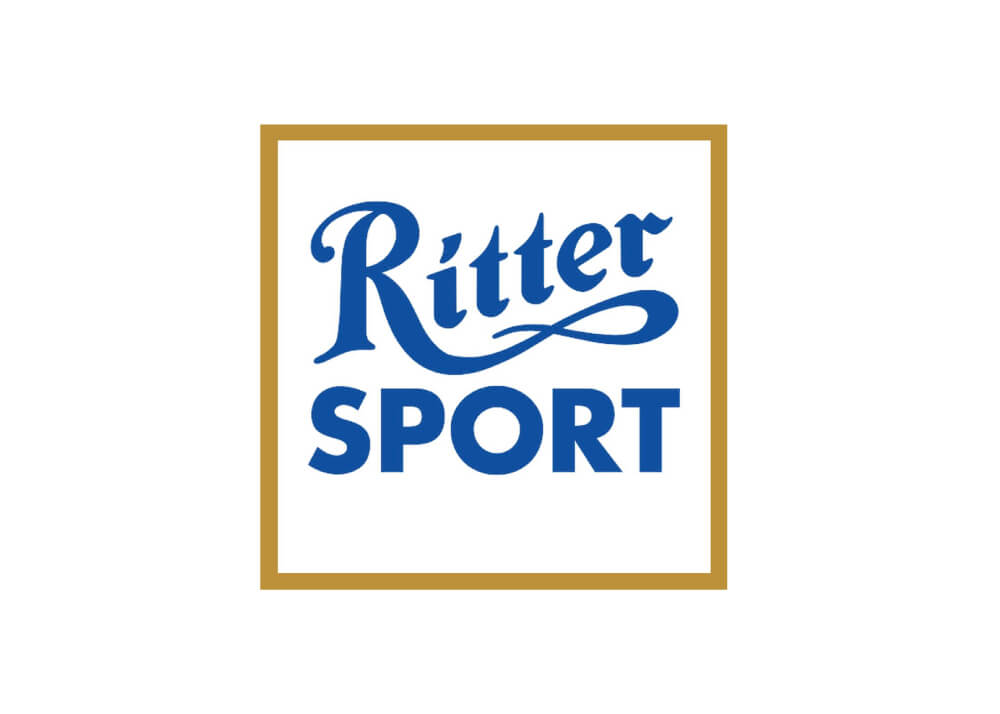
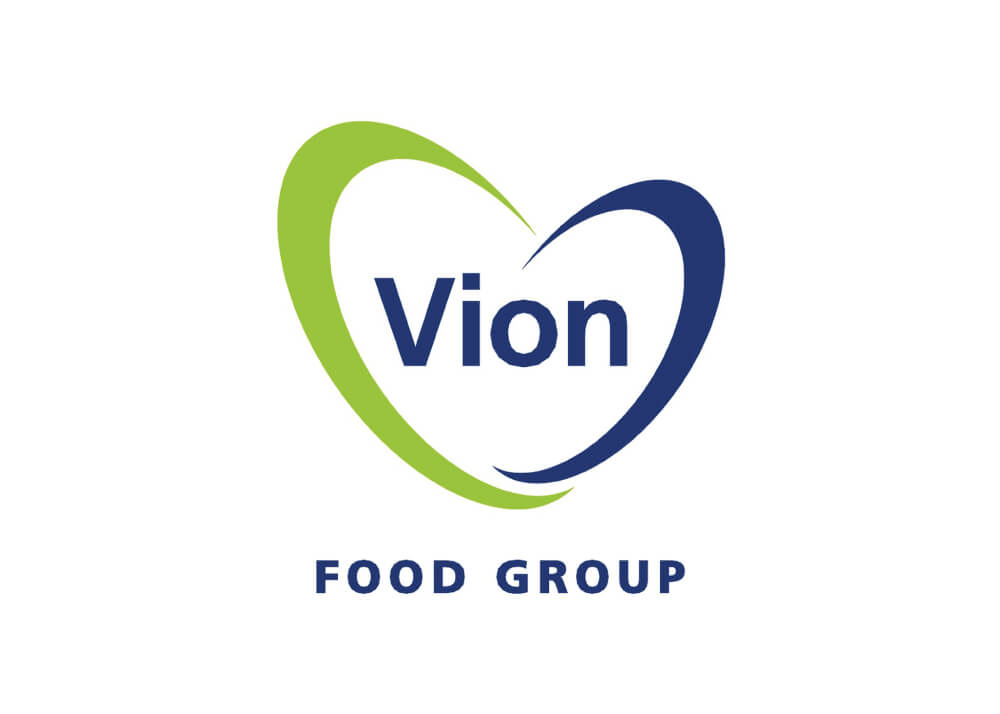
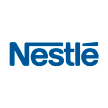
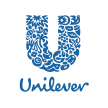
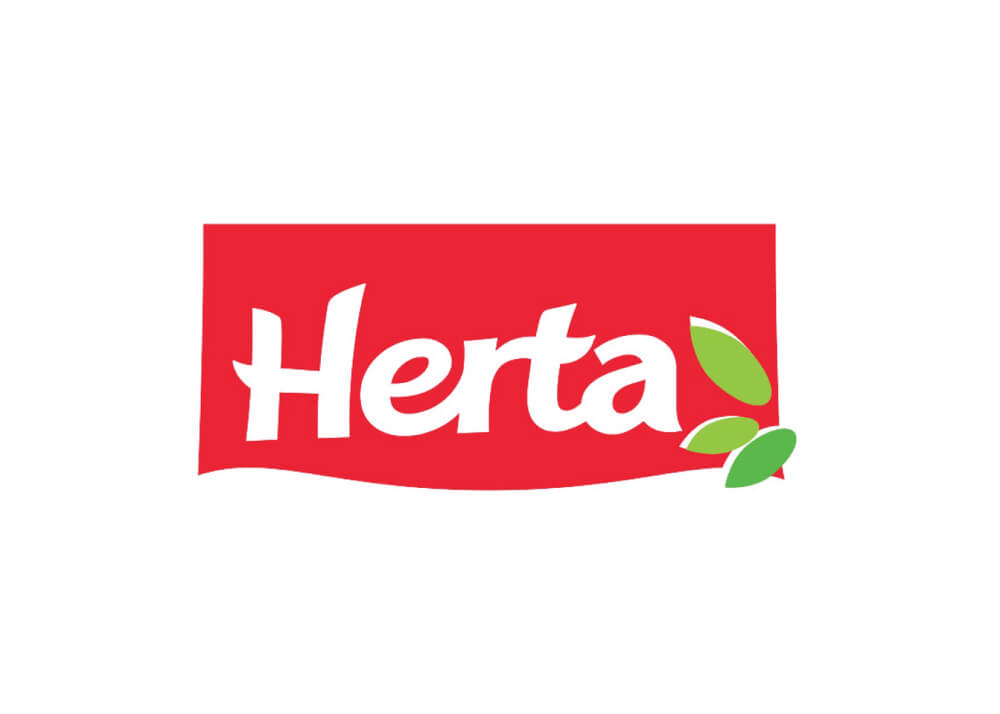
Ihre Vorteile in der Fertigungssteuerung – auf allen Ebenen
Produktionsleiter
- Minimierte Liegezeiten, Reduktion von Stillständen
- Schnelle, gezielte Reaktion auf Störungen oder Leistungsverluste
- Identifikation von Schwachstellen
- Verbesserte Auftrags- und Personalplanung
- Höherer Durchsatz durch kürzere Durchlaufzeiten
- Papierlose Fertigung
- Instandhaltungen in Produktionsabläufe integriert
- FAZIT:
Eine transparente Produktion minimiert Ihre Ressourcenverschwendung.
Nutzen für Maschinenbediener
- Stetiger Soll-/Ist-Vergleich liefert aktuelle Kennzahlen zum Auftragsfortschritt
- Einfache Erfassung aller Maschinen- und Ablaufstörungen
- Digitale Bereitstellung auftragsbezogener Dokumente sowie Überwachung wichtiger Prozessdaten
- Auftragsbuchungen direkt an der Maschine
- Anfordern der Instandhaltung bei größeren Störungen
- FAZIT:
Die digitale Überwachung des Produktionprozesses garantiert eine effiziente Arbeit an Ihren Maschinen.
Nutzen für Instandhalter
- Vorbeugende Instandhaltung ist effizient integriert
- Planung der Instandhaltung berücksichtigt die Maschinenbelegung
- Elektronische Wartungsanlagen sind vor Ort bereitgestellt
- Digitale Dokumentation aller durchgeführten Instandhaltungen inklusive Ersatzteil-Verbräuche zu allen Betriebsmitteln
- Umfassende Reports zur Analyse der Instandhaltungsmaßnahmen
- FAZIT:
Durch vorbeugende Instandhaltung und lückenlose Dokumentation sind Ihre Maschinen bestens versorgt.
Nutzen für Geschäftsführer und Controller
- Solide, aussagekräftige Datenbasis zur Unterstützung bei strategischen Entscheidungen
- Stetige Performancemessung ermöglicht aktuelle Kennzahlen
- Produktivitätspotentiale werden aufgedeckt
- Einsparungen oder Margensteigerung durch Produktionskostenreduktion
- Optimales KVP-Analysewerkzeug
- RoI in weniger als 12 Monaten
- FAZIT:
Mit digital erzeugten, aussagekräftigen Reports treffen Sie die richtigen Entscheidungen und sichern den Unternehmenserfolg.
MES-Module aus FASTEC 4 PRO
Modul Qualitätssicherung (QS)
Standard
- Verwaltung von Prüfplänen
- Live-Trigger aus MDE/BDE
- Automatische Erstellung von Prüfaufträgen
- Digitale Checklisten und Formulare
- Anbindung von Peripheriegeräten
- Proaktives Informationsmanagement
- Stichproben (SPC)
Modul Produktionsplanung (PP)
Standard
- Stammdatenverwaltung
- Artikelverwaltung
- Arbeitspläne und Stücklisten
- Fertigungsvarianten und -versionen
- Gantt-Chart mit Drag & Drop-Funktion
- Szenarien und Auswertungen
Zusatzfunktionen
- Bedarfshandling
- Digitale Plantafel
- Vorplanung
- Planungsgruppen
- Rüstregeln
- Personalverfügbarkeitsplanung
- Betriebsmittelverfügbarkeitsplanung
- Materialverfügbarkeitsplanung
- Semaphoren
- Joins
- Halbautomatische Planung
- Vollautomatische Planung
Modul Traceability (TRC)
Standard
- Erfassung von eingesetzten Komponenten
- Erfassung von Prozesswerten
- Baugruppenverwaltung
- Prozessverriegelung
- Seriennummern und Chargenverwaltung
- Etikettendruck
- Auswertungen zur Rückverfolgbarkeit
- Verwaltung von Produktionslägern
Modul Instandhaltung (INST)
Standard
- Ressourcenverwaltung
- Verwaltung von Instandhaltungsplänen
- Automatische Erstellung von Instandhaltungsaufträgen
- Digitale Formulare
- Proaktives Informationsmanagement
- Personaleinsatz- und Bedarfsplanung
- Alarmierungen
- Anfragen- und Aufgabenverwaltung
- MTBF/MTTR
- Autonome Instandhaltung
Modul Maschinendatenerfassung (MDE)
Standard
- Erfassung von Maschinenzuständen, Leistung und Qualität
- Komfortable Auswertungen
- Ausschussdifferenzierung
- Leistungsauswertung
- MTBF/MTTR
- Rüstzeitauswertung
- Zustandsauswertung
- Overall Equipment Effectiveness
(OEE) - Ressourcenlogbuch
Zusatzfunktionen
- KPI-Konfigurator
- Prozessdatenerfassung
- Prozessmeldungen
- Datenarchivierung
- Rüstregeln
Modul Betriebsdatenerfassung (BDE)
Standard
- Fertigungsauftragsmanagement
- Arbeitspläne
- Stücklisten
- Auftragsarten
- Erfassung von Mengen und Zeiten
Zusatzfunktionen
- Personalzeiterfassung
- Rezepturverwaltung (DNC/EDS)
- Dokumentenanzeige
- ERP-Buchungen
- Automatischer Auftragsstart
- Betriebsmittel-Datenerfassung
Basis-Modul
Standard
- Audit Trail
- Basis-/Stammdatenverwaltung
- Benutzer-/Rechteverwaltung
- Mehrsprachigkeit
- Report Designer
- Template Designer
Zusatzfunktionen
- Testsystem
- Alarmierungen
- OPC UA Server
- ERP-Schnittstelle
- Cloud/BI-Connector
- Online-Monitoring
- Maschinenanbindung
- Klassifizierungen
- Mobile Client
- View Client
- Office Client
