Ziel der strategischen Instandhaltung ist die Erhöhung der Zuverlässigkeit, Verfügbarkeit und Prozessstabilität des Maschinenparks, um Instandhaltungs- und Ausfallkosten zu senken sowie die Liefertermintreue zu steigern.
Realisiert werden kann dies durch effiziente, digitalisierte Instandhaltungsprozesse und optimierte Wartungsintervalle. Eine Instandhaltungssoftware, der optimalerweise in Echtzeit Maschinen- und Betriebsdaten zur Verfügung stehen, verbessert die Overall Equipment Effectiveness (OEE), ermöglicht minimalen Stillstand und entlastet das Instandhaltungspersonal. Bei der vorausschauenden Instandhaltung oder auch „Predictive Maintenance“ werden darüber hinaus Prozess- und Maschinendaten so ausgewertet, dass Prognosen möglich werden. Anlagen können proaktiv bzw. bedarfsgerecht gewartet werden, bevor eine Störung auftritt, so dass Ausfallzeiten gar nicht erst entstehen.
Potenziale und Vorteile
- Reduzierung von Kosten
- Erhöhung der Anlagenverfügbarkeit
- Vermeidung ungeplanter Stillstände
- Planbarkeit und Vereinfachung der Instandhaltungstätigkeiten
- Gezielter Einsatz und Entlastung des Instandhaltungspersonals
- Vermeidung von Verschwendung, Schonung von Ressourcen
- Digital dokumentierte Abläufe (Formulare, Checklisten, Historien)
- Basis für zukünftige KI-gestützte Prozesse
- Autonome Instandhaltung (durch digitale und zentral hinterlegte Informationen)
- Automatisierte Prozesse (Alarmierung, Anlegen von Instandhaltungsaufträgen)
- Erhöhung der Flexibilität in der Produktion
Nach wie vor hat nur ein Bruchteil (4 %) der Unternehmen die erwarteten Potenziale ausgeschöpft.*
Wie lassen sich die Potenziale realisieren?
Instandhaltung ist nicht gleich Instandhaltung. Unterschieden werden ereignisorientierte, intervall- und zustandsabhängige Instandhaltung. Zum Ziel führt oft nur ein Zusammenspiel dieser Herangehensweisen.Übersicht über die verschiedenen Herangehensweisen zur Instandhaltung. Mit einem Klick ins Bild öffnet sich eine vergrößerte Ansicht.
1. Ereignisorientierte oder reaktive Instandhaltung im Störfall
Bei der ereignisorientierten Instandhaltung wird dann reagiert, wenn bereits ein Ausfall aufgetreten ist. Entstehen bei Ausfall der Anlage keine hohen Kosten durch Folgeschäden oder Produktionsausfälle und spielt die Anwendung an der Maschine im Produktionsprozess eher eine untergeordnete Rolle, kann dies eine akzeptable Lösung sein. Dabei bildet auch die Beschaffungszeit von Ersatzteilen einen entscheidenden Faktor. Sind diese kurzfristig verfügbar, lässt sich auch die reaktive Instandhaltung effizient umsetzen.
2. Preventive Maintenance: Vorbeugende oder intervallorientierte Instandhaltung
Sind die Ausfallkosten sehr viel höher als die Kosten der Wartung, sollte das Hauptaugenmerk auf der vorbeugenden Instandhaltung liegen. Hier werden kritische Verschleißteile in festgelegten Abständen ausgetauscht. Dadurch können vorhersagbare Ausfallzeiten vermieden werden. Die vorbeugende Instandhaltung stützt sich dazu auf die durchschnittlich erwartete Lebensdauer einzelner Teile oder Anlagen, um vorauszusagen, wann eine Wartung erforderlich wird. Die Wartungen werden anhand im Vorfeld festgelegter (regelmäßiger) Intervalle durchgeführt, beispielswiese alle 300 Stunden. Basis der Instandhaltungsmaßnahmen ist also eine theoretische Ausfallrate.
Dabei wird die tatsächliche Anlagenleistung, also der tatsächliche Verschleiß, allerdings nicht berücksichtigt. Die reale Beanspruchung einer Anlage unterscheidet sich jedoch stark hinsichtlich der konkreten Nutzung, so dass es bei der vorbeugenden Instandhaltung zu unnötigen zusätzlichen Wartungsarbeiten kommen kann. Oder es werden Teile, passend zum statistischen Wartungsintervall, frühzeitig ausgetauscht und dann verschrottet, obwohl diese noch einwandfrei funktionieren. Dies ist kostenintensiv und steht nicht im Gedanken der Nachhaltigkeit und Ressourcenschonung.
3. Predictive Maintenance: Vorausschauende oder zustandsabhängige Instandhaltung
Bei der zustandsabhängigen Instandhaltung sollen Maschinenteile so lange wie möglich genutzt und erst kurz vor deren absehbarem Ausfall ausgetauscht werden. Beispielsweise werden einzelne Bereiche der Anlage an produktionskritischen Stellen im laufenden Betrieb digital über Sensoren überwacht. Die Sensoren kontrollieren den Maschinenzustand über die Messung von Temperatur, Schwingung, Luftfeuchtigkeit und Druck. Abweichungen z. B. in der Schwingung sind ein Indikator für den baldigen Verschleiß eines Maschinenteils. Die Maschinen sind miteinander verknüpft, wodurch eine rechtzeitige Identifikation von Fehlerquellen und ein zeitnahes Eingreifen möglich wird. Störungen können so mit hoher Treffsicherheit diagnostiziert und Wartungen und Maschinenstillstände genau geplant werden. Auch live über die Maschinendatenerfassung (MDE) aus der Maschine ausgelesene Daten wie Zustände, Laufzeit oder Stückzahl können dazu herangezogen werden. Anhand dieser Echtzeitdaten wird der Zustand vom in Betrieb befindlichen Maschinen bestimmt, um vorauszusagen, wann eine Wartung durchgeführt werden sollte. Aufträge können dann automatisch generiert werden.
Hauptziel von Predictive Maintenance ist die möglichst präzise Vorausplanung der Instandhaltung, um unerwartete Ausfälle von Anlagen und somit unnötige Kosten zu vermeiden. Mit dem Wissen, wann welche Maschinen oder einzelne Teile gewartet werden müssen, lassen sich Ressourcen für Instandhaltungsarbeiten wie Ersatzteile oder Arbeitszeiten besser planen. Zudem kann die Anlagenverfügbarkeit erhöht werden, indem „ungeplante Stopps“ in immer kürzere und häufigere „geplante Stopps“ umgewandelt werden. Zusätzliche Chancen sind eine potenziell längere Lebensdauer der Maschinen, erhöhte Anlagensicherheit, Reduzierung von Unfällen mit negativen Auswirkungen auf Mitarbeitende oder die Umwelt sowie ein optimiertes Ersatzteilhandling.
Die Bedeutung des Zusammenspiels von Maschinendatenerfassung (MDE), Betriebsdatenerfassung (BDE) und Instandhaltung:
Mit kontinuierlicher Datenerfassung, Datenauswertung und einer vollständigen Vernetzung der Anlagen kommen Unternehmen der fertigenden Industrie ihrem Ziel einer nahezu stillstandslosen Fertigung (Zero-Downtime) bereits sehr nah. Ob Predictive Maintenance funktioniert, hängt jedoch stark von der zur Verfügung stehenden Datenqualität ab. Relevante Daten zu erheben, auszuwerten und Wartungsintervalle zu automatisieren, dafür stellen Manufacturing Execution Systeme (MES) mit Modulen zur Maschinendatenerfassung (MDE) oder Betriebsdatenerfassung (BDE) etc. eine wichtige Voraussetzung dar. Ist die Instandhaltungssoftware Bestandteil einer MES-Softwarelösung kann auf eine große Datenfülle qualitativer Maschinendaten zugegriffen werden – und dies in Form von Echtzeitdaten sowie in Form historischer Daten, da die erfassten Daten automatisch digital dokumentiert werden. Durch die Vernetzung werden z. B. Zustandsdaten, Verbrauchs- und Verschleißwerte erfasst, die ein sehr genaues Bild vom Zustand der Anlagen und der produzierten Teile vermitteln. Sinnvoll kombiniert mit Daten aus dem MES- und ERP-System können Wartungszeitpunkte einer Anlage präzise prognostiziert werden. Die Software steuert durchgehend den Maschinen- und Werkzeugeinsatz und erinnert den Instandhalter selbständig an anstehende Wartungen. Starr eingeplante, regelmäßige Wartungsintervalle werden durchbrochen und der Instandhalter kann bereits einschreiten, bevor die Produktivität der Maschinen abzunehmen droht – oder erst dann, wenn es wirklich notwendig ist.Umfangreiche Vorteile durch gemeinsame Datenbasis
- Bestehende Ressourcen wie Personalgruppen, Betriebsmittel und Arbeitsplätze/Linien sind in der gesamten Produktionsumgebung ohne Schnittstellen oder doppelte Datenhaltung nutzbar
- Der Maschinenbediener wählt einen vordefinierten Zustand aus. Dadurch wird automatisch ein Instandhaltungsauftrag angelegt sowie Alarmierungen an beteiligte Personen/Fachabteilungen gesendet
- Beim Starten einer Wartung durch den Instandhalter wird automatisch der passende Maschinenzustand ausgelöst und von der MDE erfasst
Vorteile einer digitalen Instandhaltung
- Verbesserung der Wirtschaftlichkeit:
- Verringerung von Stillstandszeiten
- Reduzierung von Kosten für ungeplante Ausfälle
- Erhöhung der Lebensdauer von Maschinen und Anlagen durch regelmäßige bedarfsorientierte Wartung
- Bessere Vorhersagen bei Ersatzteilmanagement
- Optimaler Wartungszeitpunkt, Vermeidung von Ausfällen:
- für die Anlage durch permanente Auswertung der Maschinendaten
- innerhalb des Produktionsprozesses durch Planung
- Erhöhung der Flexibilität in der Produktion
- Verbesserung der Maschinenleistung:
- durch permanente Analyse der gesammelten Daten
- Langfristig Erzielung einer höheren Produktivität
- Schnellere Fehlerfindung und Reaktion bei Störungen
Die im Rahmen dieser Projekte erzielten Ergebnisse übertrafen die Erwartungen zum Teil deutlich. In den Bereichen Wartungs-/Servicekosten und Anlagenstillstandszeiten konnten Reduzierungen von 17 bzw. 18 % erreicht werden und Umsätze um 10 % gesteigert werden.*
Blick in die Praxis
1) Autonome Instandhaltung – mehr Verantwortung für den Maschinenbediener
Instandhaltungsprozesse werden durch die Bereitstellung unterstützender Dokumente wie Checklisten und autonomer Instandhaltungspläne vereinfacht und vereinheitlicht. Dadurch können kleinere Maßnahmen wie Reinigen, Ölen oder andere Tätigkeiten an der Maschine direkt an den Maschinenbediener übertragen werden. Diese gezielte Übertragung der Verantwortung spart Zeit und Kosten und erhöht die Identifikation des Maschinenbedieners mit dem Produktionsprozess. Im Ergebnis wird der Produktionsablauf beschleunigt, da nicht mehr für jede kleine Wartungsmaßnahme ein Instandhalter eingebunden werden muss. Autonome Instandhaltungen können zudem schnell konfiguriert werden, inklusive Sicherstellung einer durchgehenden Dokumentation.
Zusätzlich haben die Maschinenbediener im Kontext der Total Productive Maintenance (TPM) jederzeit die Möglichkeit, Verbesserungsvorschläge und Anmerkungen im System zu hinterlegen. TPM-Verantwortliche haben durch die einheitliche Maßnahmenverwaltung und durch geregelte Abläufe für Mängelhinweise und Instandhaltungsanfragen eine valide Grundlage, um die Umsetzung der vorgeschlagenen Maßnahmen zu prüfen und kontinuierliche Verbesserungen im Maschinenpark zu erreichen.
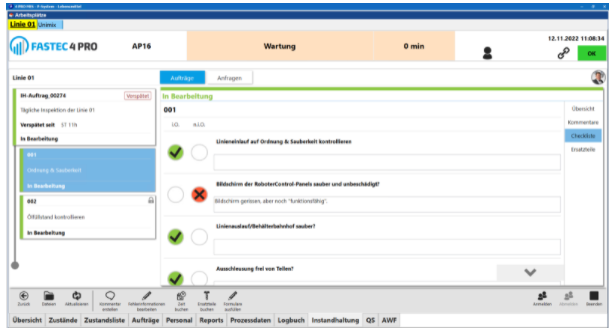
2) Optimierungen nach kurzer Zeit spürbar
Viele unserer Kunden berichten nach der Einführung des FASTEC 4 PRO Instandhaltungsmoduls von direkt spürbaren Verbesserungen basierend auf der produktionsweit einheitlichen Datenbasis. Händische Dokumentationen von Wartungen in Papierform oder Excel-Dateien wurden abgeschafft, was zu Kosten und Zeiteinsparungen durch den Wegfall manueller Prozesse führte. Bei Anfragen durch Vorgesetzte oder externe Prüfungen sind die benötigten Dokumente jetzt überall per Knopfdruck verfügbar. Mitarbeitende in der Produktion nutzen nun Tablets, um die Datenlage und den Status der Anlagen in Echtzeit zu überblicken. Außerdem können Sie die Tablets direkt mit an und sogar in die Maschine nehmen, um alle benötigten Informationen wie Checklisten, Betriebsanleitungen oder Bilder in den Dokumenten für Ausbauanleitung etc. zur Hand zu haben. Bei regelmäßig anfallenden Wartungsarbeiten, bspw. jährlich, ist im System immer erkennbar, wann die letzte Wartung durchgeführt wurde und wann die nächste fällig ist. Insgesamt wurde die Instandhaltung durch papierlose Prozesse effizienter und effektiver, dadurch gab es ebenfalls weniger Unterbrechungen im Produktionsablauf, was zur allgemeinen Steigerung der Produktionseffizienz beiträgt.
Ausblick – der nächste Schritt auf dem Weg der digitalen Transformation: Predictive Analytics
Um verlässliche Aussagen über den Zustand von Maschinen und Anlagen machen und dadurch zu erwartende Störungen identifizieren zu können, ist es notwendig große Mengen an Daten mit Softwarelösungen wie FASTEC 4 PRO über einen längeren Zeitraum zu erheben.
Durch BI-Tools und Datenanalyse werden Szenarien der Vergangenheit analysiert, um Fehlerquellen zu identifizieren und zukünftig Verbesserungen zu implementieren. In Kombination mit Künstlicher Intelligenz ergibt sich bei Predictive Analytics die Möglichkeit, Störungen zu vermeiden lange bevor diese eintreten. Basierend auf historischen Daten werden Vorhersagen über Ereignisse in der Zukunft möglich, die auf bestimmte Konstellationen von Parametern zurückzuführen sind (z. B. Einstellungen bei Maschinen in der Produktion). Eine solide Grundlage digital erfasster Produktionsdaten (MDE, BDE, Instandhaltung) ist daher Voraussetzung für zukünftige KI-Projekte. Je größer die Datenbasis und je intelligenter und ausgefeilter der Algorithmus ist, desto verlässlicher sind die Erkenntnisse.
Handlungsempfehlungen
- Start mit kleinen, fokussierten Projekten zu einer kritischen Anlage oder einem kritischen Prozess
- Datenelemente und technische Voraussetzungen für den Anwendungsfall definieren
- Sammeln relevanter Daten
- Iterative Optimierungen
- Ausgewählte Anlagen schrittweise skalieren
- Relevante Anlagen nachrüsten, um weitere Daten zu sammeln und weitere Optimierungen umzusetzen
- Aufbau von Know-how (intern, extern)
- IT-Sicherheit berücksichtigen, um unbefugten Zugriff zu verhindern
* Quelle: Predictive maintenance Studie 2021, Bearing Point
https://www.bearingpoint.com/de-de/insights-events/insights/chancen-und-herausforderungen-von-predictive-maintenance-in-der-industrie/