Expertise and Solutions for Plastics Processing
Our customers are specialized in the most common methods of plastics processing, namely injection molding and extrusion. In some cases, more than 100 machines are connected to our MES at one location. What would you like to optimize in your production?
Your Digitalization Partner in the Plastics Processing Industry
Nowadays, plastic can be found in almost all areas of life. Whether in the form of mass-produced articles for the consumer market or in the form of sophisticated medical products. However, they all have one thing in common: Our MES system FASTEC 4 PRO can be found in many plastics processing companies. The area of application ranges from simple Machine Data Acquisition including online monitoring to Process Data Acquisition and to Detailed Scheduling taking into account tool availability. FASTEC 4 PRO also supports the definition and planning of conversion tools.
The complete documentation of a batch is particularly important in the production of medical products. Our QA module takes over exactly this function: Starting with the upload/download of setting data records, any number of process parameters is stored for each shot. Similarly, every single parameter change made by the machine operator is also stored in a database (set-up log). The machines are connected – according to requirements – via simple digital signals up to more powerful Euromap 63 or OPC UA interfaces.
Selection of Our Customers in the Plastics Processing Industry
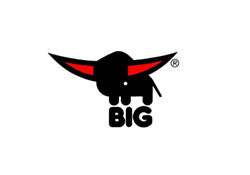
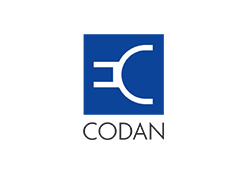
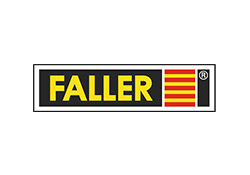
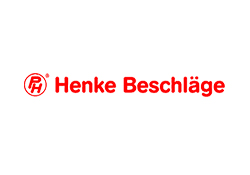
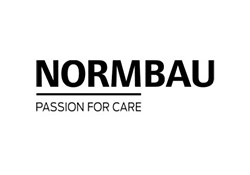
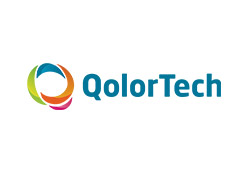
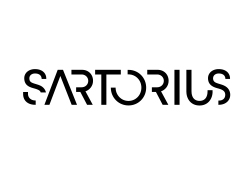
At a Glance
For each tool, the current status can be maintained. This allows you to easily identify the tools that require inspection and thus preventing them from being used on the machine.
In injection molding production, one setter is often responsible for several machines. Due to the dense machine layout, it is often difficult to see whether all machines are running. With our Mobile Client, the setter can be informed immediately if the machine is no longer running in its cycle or even stops completely. In addition, downtimes and their causes can also be entered via the Mobile Client. This saves you money that you would have to spend on additional terminal hardware.
For each article to be produced, a setting data record can be stored for each machine. The next time this article is produced, it is automatically loaded into the machine. If parameter changes are made during production, these are stored in the order documentation and are available at all workstations in a standardized form at all times. At the end of production, you can chose and decide whether the changed data record is uploaded to the server and thus becomes the new master data record.
Contract injection molders in particular are interested in producing with the lowest possible factor input. What is more, energy consumption also plays a decisive role here, especially in injection molding production. With our additional function Energy Monitoring, the consumption during production is recorded and stored order- or article-related. This means that the energy consumption for each part produced can easily be calculated for post calculation.
To implement a simple MDA system, only one digital clock signal is required for each machine. This can be used to calculate the number of shots for each order, the cycle time as well as the machine status. However, if process values or rather the set-up log is to be read out of the machine or setting data records are to be transferred, real data interfaces are required.
Telephone: +49 5251 1647-0
or via the Contact Form
"The decisive factor in choosing FASTEC 4 PRO was the flexible connection concept, which guaranteed a fast and cost-efficient implementation in our company."
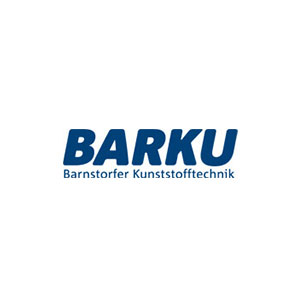
Your Advantages in Production Control – at All Levels
Benefits for Production Managers
- Minimized idle times, reduction of downtimes
- Fast, targeted response to disturbances or performance losses
- Identification of deficiencies
- Improved order and personnel planning
- Higher throughput thanks to shorter processing times
- Paperless production
- Maintenance integrated into production processes
- CONCLUSION: A transparent production minimizes your waste of resources.
Benefits for Machine Operators
- Continuous target/actual comparison provides up-to-date key figures on order progress
- Simple recording of all machine and process disturbances
- Digital provision of order-related documents and monitoring of important process data
- Order bookings directly at the machine
- Requesting maintenance in the event of major disturbances
- CONCLUSION: Digital monitoring of the production process guarantees efficient operation of your machines.
Benefits for Maintenance Staff
- Preventive maintenance is effectively integrated
- Planning of maintenance takes into account machine utilization
- Electronic maintenance facilities are provided on site
- Digital documentation of all maintenance work carried out, including spare parts consumption for all operating resources
- Comprehensive reports for analysis of maintenance measures
- CONCLUSION: Preventive maintenance and complete, seamless documentation ensure that your machines are well taken care of.
Benefits for Managers and Controllers
- Reliable, meaningful database to support strategic decisions
- Continuous performance measurement enables up-to-date key figures
- Productivity potentials are revealed
- Savings or margin increase by reducing production costs
- Optimal CIP analysis tool
- ROI in less than 12 months
- CONCLUSION: With digitally generated, meaningful reports, you make the right decisions and ensure your company's success.
MES Modules From FASTEC 4 PRO
Quality Assurance Module (QA)
Standard
- Management of test plans
- Live trigger from MDA/PDA
- Automatic creation of test orders
- Digital checklists and forms
- Binding of peripheral devices
- Proactive information management
- Statistical process control (SPC)
Production Planning Module (PP)
Standard
- Master data management
- Article management
- Routings and bills of materials
- Production variants and versions
- Gantt chart with drag & drop function
- Scenarios and analyses
- Demand handling
- Digital planning board
- Preplanning
- Planning groups
- Setup rules
- Personnel availability planning
- Equipment availability planning
- Material availability planning
- Semaphores
- Joins
- Semi-automatic planning
- Fully automatic planning
Traceability Module (TRC)
Standard
- Acquisition of components used
- Acquisition of process values
- Assembly management
- Process locking
- Serial numbers and batch management
- Label printing
- Reports for traceability
Additional Functions
- Management of production warehouses
Maintenance Module (M)
Standard
- Resource management
- Maintenance plan management
- Live trigger from MDA/PDA
- Automatic creation of maintenance orders
- Digital forms
- Proactive information management
- Personnel deployment and requirements planning
- Alerts
- Request and task management
- MTBF/MTTR
- Autonomous maintenance
Machine Data Acquisition Module (MDA)
Standard
- Recording of machine conditions, performance and quality
- Convenient reporting:
- differentiation of rejects
- performance analysis
- MTBF/MTRR
- setup time report
- states reports
- Overall equipment effectiveness (OEE)
- Resource Log
Additional Functions
- KPI Configurator
- Process data acquisition
- Process messages
- Data archiving
- Setup rules
Production Data Aquisition Module (PDA)
Standard
- Production order management
- Routings
- Bill of material
- Various order types
- Acquisition of quantities and times
- Staff time recording
- Formula management (DNC/EDS)
- Document display
- ERP bookings
- Automatic order start
- Equipment data acquisition
Basic Module
Standard
- Audit trail
- Basic/Master data management
- User/rights management
- Multilingualism
- Report Designer
- Template Designer
Additional Functions
- Test system
- Alerts
- OPC UA Server
- ERP interface
- Cloud/BI-Connector
- Online monitoring
- Machine connection
- Classifications
- Mobile Client
- View Client
- Office Client
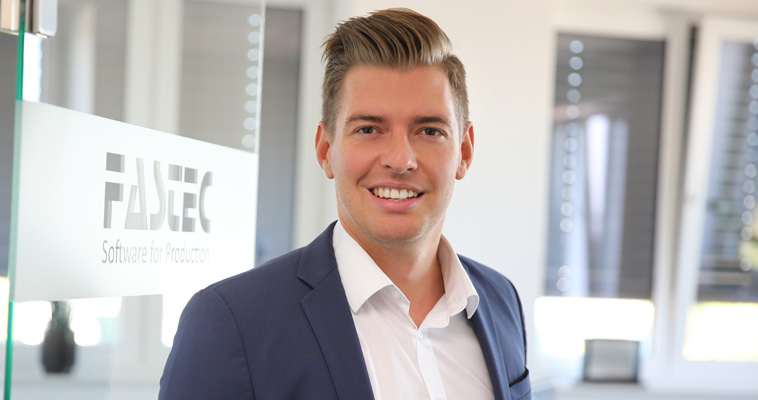
Are You Interested in or Have Questions About Solutions for Your Company?
We provide customized solutions. With us, you benefit from extensive project experience in digital production in various industries. With over 400 customers. Worldwide. Our consultants can draw on many years of experience from diverse customer projects and can often identify optimization potentials at first glance. In this way we offer you individual, tailor-made solutions. For more than 25 years.