User Report NORMBAU
MES Solution FASTEC 4 PRO at NORMBAU GmbH in Renchen in the Black Forest.
The full report is available for download.
The FASTEC 4 PRO Software Solution at NORMBAU
Since its foundation in 1954, NORMBAU has developed from a family business into a manufacturer and worldwide supplier of high-quality, accessible and sanitary equipment series, building hardware and electronic access control systems. Since December 2013, the company has been part of the Allegion Group.
Manual data acquisition and reports took an extremely long time at NORMBAU. Manually recorded or estimated scrap served as the basis for quality indicators, which were consequently not very representative. In order to achieve greater transparency and to calculate the OEE key figure regularly and accurately, NORMBAU decided as early as 2010 to gradually digitalize its production. By 2011, modules of the FASTEC 4 PRO software had been rolled out across the group.
- Industry: plastics processing
- Goal: Station by station to fully digitized production
- In Use: FASTEC 4 PRO software solution with the modules and additional functions MDA, PDA, maintenance, detailed scheduling, alerting, monitoring, document display and personnel time planning
"In the past, we could only determine electricity consumption per building. Thanks to FASTEC 4 PRO, we are now also able to evaluate consumption per machine and per order."
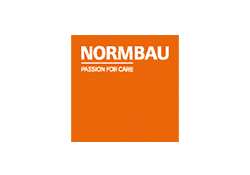
"In my opinion, there is no other option these days than to use digital systems such as FASTEC 4 PRO for production optimization. Otherwise you would lose touch with the competition. FASTEC is the ideal partner for this approach."
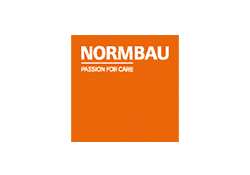
"Manual data acquisition and evaluation has long since become outdated and we are happy to have made an early start on digitalized production."
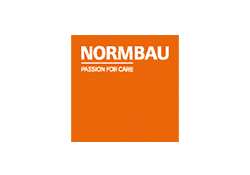
Short and Precise
Digitalization as a Journey:
After a 6-month test phase with easyOEE in 2009, NORMBAU decided to digitize its manufacturing processes with FASTEC 4 PRO in 2010 and rolled it out across the group in 2011. Since then, the modular software solution has been expanded step by step to Detailed Scheduling.
90% Less Paperwork and Real-Time Data Are Convincing:
Previously, NORMBAU maintained 1,500 order folders for 1,600 different items manually – a high personnel and time effort that was costly, inflexible and confusing. All documents were digitized with FASTEC 4 PRO and new content can now be entered directly into the database. The conversion to automatic order registration was quick. Barcodes generated by the ERP system can now be scanned at the terminal or machine. The View Client of the Additional Function Monitoring is also in use. The current production status is always clearly displayed on large screens in production. In particular, work centers, items, target and actual quantities, OEE, current progress, quality in percent and the current state are displayed. An automatic page change is integrated to provide an overview of the entire production.
Optimized Planning as the Key to Success:
Before the introduction of the FASTEC 4 PRO Detailed Scheduling module in 2019, the various planning steps were still carried out manually. The challenges of the project were a high complexity due to quantities of 10 to 20,000 per Production order with 10,600 different items in eleven colors, as well as a large quantity of tools with one or two parts, which can be produced either together or only separately. Thanks to FASTEC 4 PRO, NORMBAU has a freely configurable tool tip for every planning order, which outputs order data as well as order deadlines or other information at the click of a mouse.

Do You Have Special Requirements for Digital Production Management?
No problem. We deliver customized solutions. With us, you benefit from extensive project experience in digital manufacturing in various industries. With over 400 customers. Worldwide. Since 1995.
Who We Work For
From automotive suppliers to food producers, pharmaceutical companies to toy manufacturers, from highly specialized niche suppliers to ambitious medium-sized companies to large international corporations – over 400 customers around the globe rely on Software for Production – made in Paderborn. Among them:
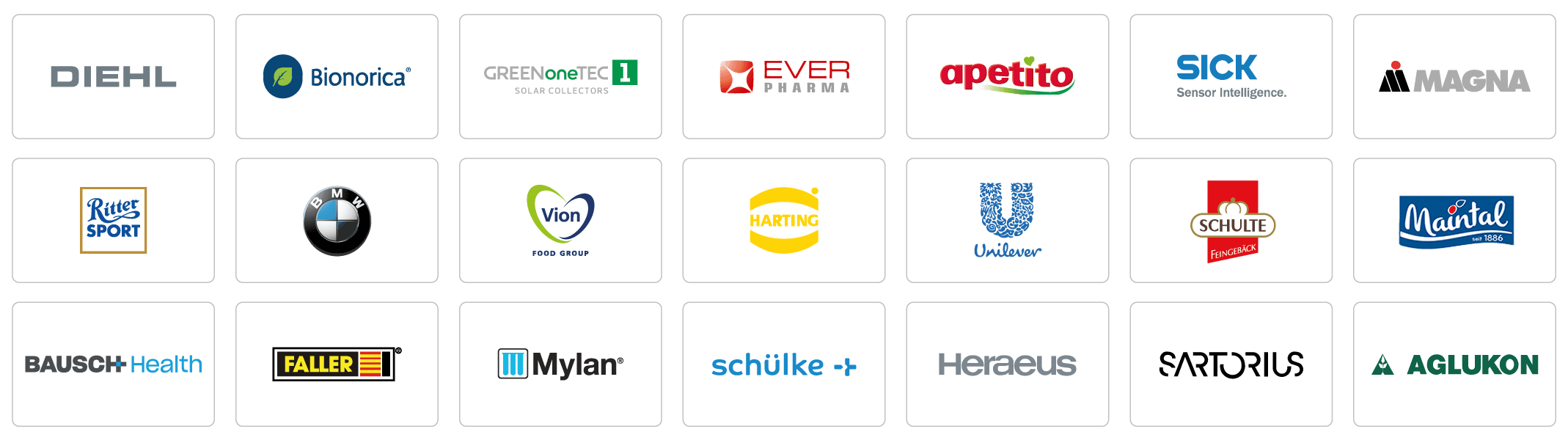
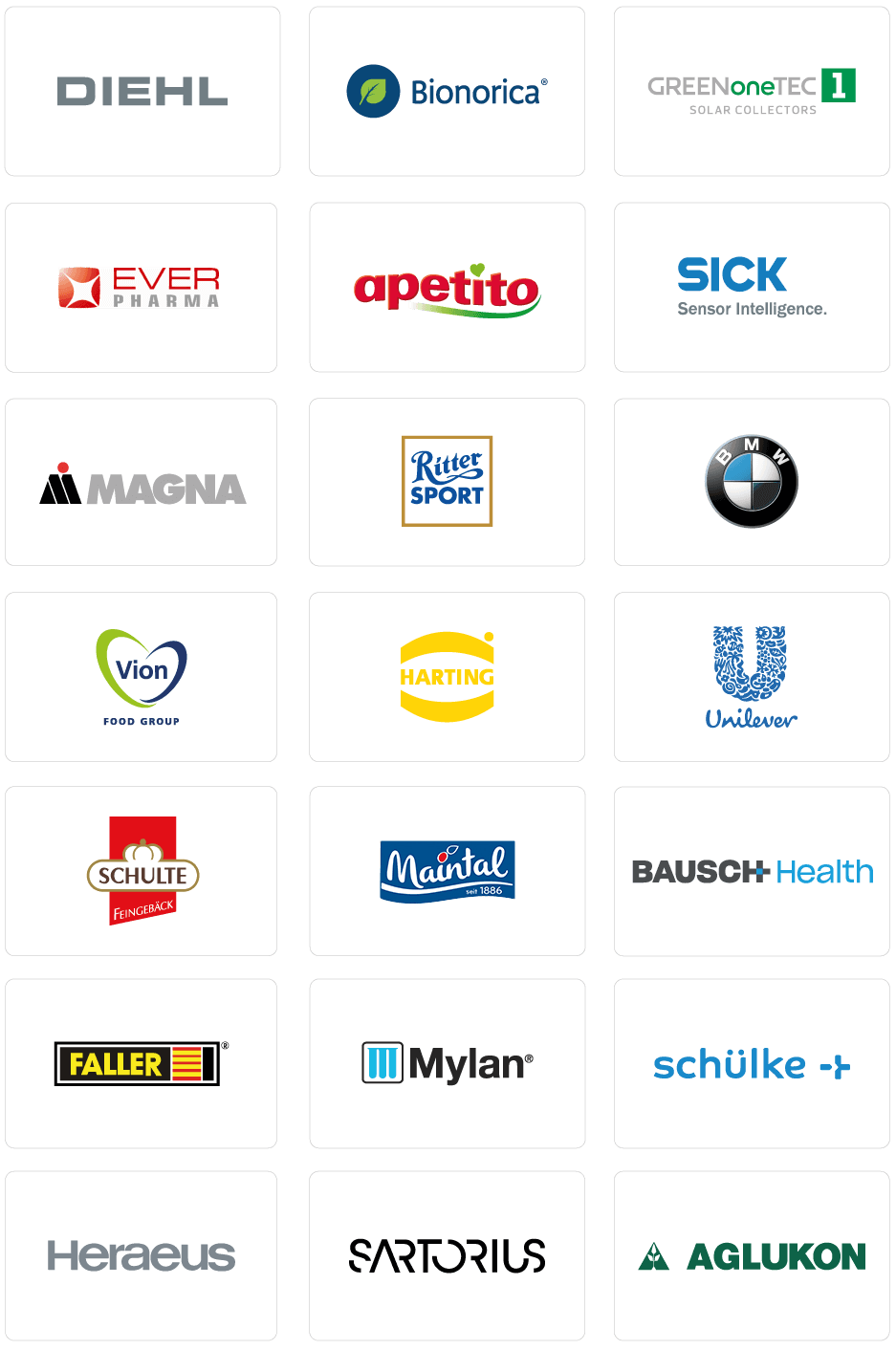