Optimierte Prozesse, flexibles Reagieren, Daten in Echtzeit – die intelligente Fabrik steht im Mittelpunkt der digitalen Transformation fertigender Unternehmen. Die Herausforderungen sind enorm. Als Schlüssel zur langfristigen Sicherung der Wettbewerbsfähigkeit spielt neben der Entwicklung neuer Produkte oder der Investition in zukunftsfähige Technologien besonders die digitalisierte Produktion eine entscheidende Rolle, um sich zukunftsfähig aufzustellen.
Unternehmen mit einem hohen Digitalisierungsgrad stehen besser da, nicht nur in pandemischen Zeiten. Schon in der Finanz- und Wirtschaftskrise von 2008/2009 waren hoch digitalisierte Unternehmen eindeutig im Vorteil, wie eine Studie des ZEW Mannheim belegt. Produktivitätsniveau und -wachstum blieben bei diesen Unternehmen nahezu konstant. Bei weniger digitalisierten Unternehmen gingen diese hingegen stark zurück. Die digitalen Vorreiter waren zudem auch eher in der Lage, flexibel zu reagieren, Prozessinnovationen umzusetzen oder Kosten einzusparen. Sie waren resilienter.
Doch in vielen Industrieunternehmen sieht die Situation noch ganz anders aus. In der Fertigung sorgen historisch gewachsene IT-Insellösungen für Daten-Chaos. Dadurch können diese Unternehmen trotz Nutzung von IT-Anwendungen nicht flexibel genug auf Störungen wie kurzfristige Auftragsänderungen im Fertigungsprozess reagieren. Sie greifen bei ihrer operativen Planung deshalb oft noch auf eigenentwickelte Systeme oder Excel- und Papierdokumentation zurück. In der Folge können Produktionsprozesse nicht effizient geplant, abgewickelt oder rückverfolgt werden. Flexible Anpassungen an Ereignisse – zum Beispiel in der Planung – sind nicht oder lediglich mit hohem Aufwand und zeitlich verzögert möglich. Die Rückmeldungen ins ERP-System erfolgen dann häufig nur einmal pro Schicht oder am Ende eines Auftrags. Auf die für das Tagesgeschäft wichtigen Fragen können dadurch keine spontanen Antworten gegeben werden. Eine smarte/intelligente Produktion scheint unerreichbar.
Fertigungsunternehmen mit geringerer Variantenvielfalt und Automatisierung konnten in der Vergangenheit die Feinplanung händisch bewältigen und sich dabei auf langjährige Erfahrung der Mitarbeiter verlassen. Aufgrund der heutigen Datenfülle und Komplexität ist dies nicht mehr möglich.
Der Weg zur Smart Factory erscheint für viele Unternehmen noch weit.
Die Vision: Eine intelligente, in beteiligten Ressourcen und Systemen vernetzte Fabrik. Jede Maschine kennt ihre Aufträge, Bauteile kommunizieren untereinander über ihre Bestimmungsziele. Das Produkt findet seinen Weg durch den Shopfloor, um schließlich direkt zum Auftraggeber zu gelangen – so die Idee. Auch wenn einige Unternehmen mit Modellfabriken diesem Bild bereits nahekommen, ist es fraglich, ob bzw. wann dieses Ideal die Norm deutscher Fabriken darstellen wird und muss.
Sicher ist jedoch, dass produzierende Unternehmen ihre Fertigung flexibler, nachhaltiger und reaktionsfähiger gestalten müssen.
Je transparenter komplexe Prozesse erfasst werden, desto schneller und fundierter können Unternehmen bei Störungen oder veränderten externen Rahmenbedingungen reagieren.
Der Beitrag des MES – Erfassung und Einbindung relevanter Informationen in Echtzeit
Ein Manufacturing Execution System (MES) ist ein System im operativen Produktions-management und unterstützt bei Aufgaben wie Produktionsplanung und -steuerung. Zu den Hauptaufgaben von MES gehören z.B. Feinplanung, Qualitätssicherung oder Instandhaltung. Das MES stellt ein digitales Abbild der Produktion zur Verfügung und ermöglicht die Überwachung der Produktionsprozesse in Echtzeit
Durch die Möglichkeit umfangreiche und vielfältige Daten zu erfassen, bildet das MES eine Datendrehscheibe, die eine horizontale Integration ermöglicht. Echtzeit-Informationen zu Aufträgen und Ressourcen werden über Betriebs- und Maschinendatenerfassung im MES erfasst, verarbeitet und gespeichert – im Normal-/Regelbetrieb, aber auch im Falle von auftretenden Störungen.
Neben einer horizontalen Integration ermöglicht das MES auch die Integration in vertikaler Richtung. MES sind also das Bindeglied zwischen dem ERP-System sowie der Maschinen- und Ausführungsebene des Produktionsprozesses. So entsteht durchgehende Transparenz über aktuelle und anstehende Aufträge sowie Ressourcenzustände.
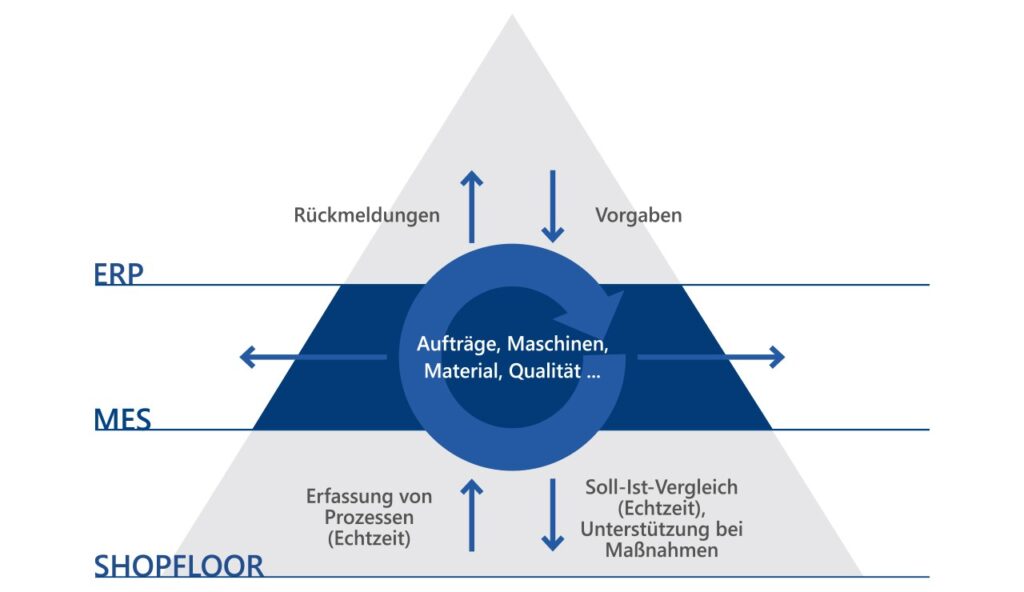
MES als Datendrehscheibe zwischen ERP- und Shopfloorebene (horizontal und vertikal integriert)
MES sind multifunktionale Anwendungen, die als Verschmelzung vieler, zum Teil individueller Systeme zu verstehen sind, welche vorher häufig als Insellösungen realisiert wurden. Mit den vom MES digital und systematisch erfassten Daten, können Schwachstellen aufgedeckt, Mitarbeiter unterstützt, durchgängige Informationsflüsse gestaltet, vorausschauend reagiert und Abläufe dauerhaft verbessert werden.
Transparente Daten in Echtzeit bilden die Grundlage, um Fragen nach Produktionseffizienz oder Kapazitätsauslastungen mit den technischen Möglichkeiten der Produktionsanlagen zu kombinieren. Nur dann sind faktenbasierte Entscheidungen möglich, um bestehende Prozesse zu optimieren und die Zukunft der Fertigung im Unternehmen aktiv zu gestalten.
MES als wichtiger Schritt beim Einstieg in Richtung Smart Factory
Mit einem MES stehen Daten an jedem Ort der Fertigung zur Verfügung und lassen sich für alle Prozesse untereinander verknüpfen. Als zentrales Informationssystem im Werk übernimmt der Rollout eines MES daher eine Schlüsselrolle beim Einstieg in die Digitale Transformation. MES legt die Basis auf dem Weg zu Industrie 4.0, KI, Machine Learning, digitale Zwillinge, Cloud, Digitalisierung und IIoT. Alle diese Technologien tragen zum größeren Ziel ‚Smart Factory’ bei. Dieses kann man jedoch nur schrittweise erreichen – individuell und mit einem strategischen Fahrplan.
Die gewonnene Reaktionsfähigkeit und die resultierende Flexibilität schlagen sich jedoch auch schon vorher nieder; monetär in einer Steigerung der Maschinen- und Anlageneffizienz, einer Reduzierung der Durchlaufzeiten und Bestände oder auch einer Steigerung der Prozesssicherheit und Entlastung der Mitarbeitenden.