Hemmnisse der digitalen Transformation
In turbulenten Zeiten ist es besonders wichtig, nicht am Status-Quo festzuhalten, um die Chancen in der Digitalen Transformation für das eigene Unternehmen zu erkennen und den Prozess anzugehen. Zentrale Hemmnisse sind dabei häufig:- Hemmnis 1: Unklares Kosten-Nutzen-Verhältnis: Fehlende Transparenz bezüglich der Potenziale in der Produktion
- Hemmnis 2: Abstrakte Informationen, unklarer Praxisbezug und fehlendes Konzept
Lösung 1: Optimierungspotenziale im Vorfeld einer Investition aufdecken und ROI berechnen
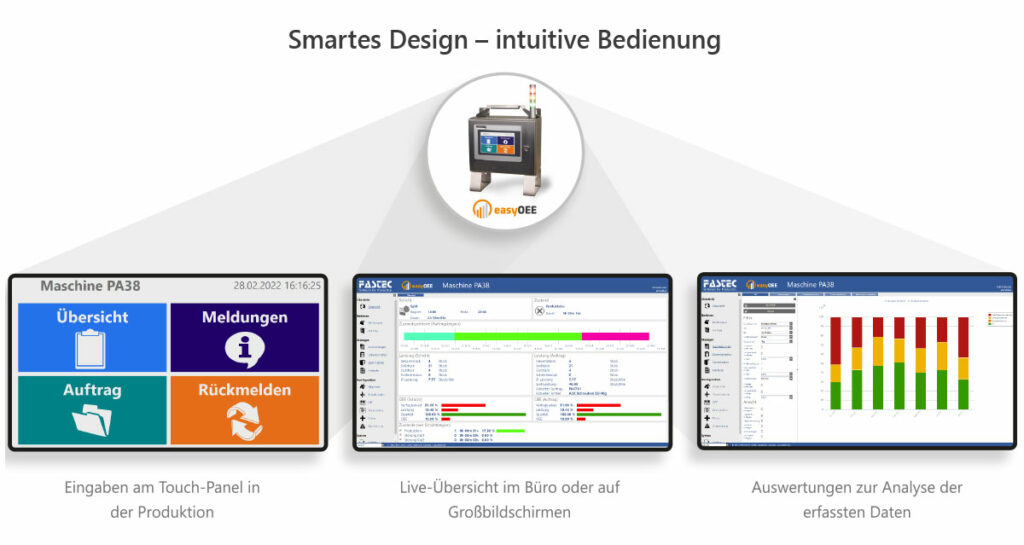
Mit unserem Produktivitätsmessgerät easyOEE treffen Sie Investitionsentscheidungen auf Basis valider Daten und real identifizierter Potenziale.
easyOEE erfasst über digitale Signale die Maschinendaten zur Leistung, Verfügbarkeit und Qualität einer Anlage und errechnet den OEE-Wert. Auf Basis der Potenziale kann eine ROI-Berechnung die Investition in das MES FASTEC 4 PRO rechtfertigen.
Das Produktivitätsmessgerät easyOEE wird an einer Maschine angeschlossen. Ihr Elektriker kann vorhandene digitale Signale verarbeiten oder eine Lichtschranke montieren. Die Konfiguration erfolgt auf Basis Ihrer Stammdaten.
Der Maschinenbediener meldet zum Start der Produktion einen Fertigungsauftrag am Gerät an. Anschließend erfasst easyOEE Stückzahlen und Produktionszeiten automatisch. Sobald ein Stillstand anliegt, wählt der Maschinenbediener den Grund der Störung aus einer vorkonfigurierten Liste aus und kann diesen durch Freitexte verfeinern. Ebenfalls besteht die Möglichkeit, technische Störungen der Maschine automatisiert zu verarbeiten. Die Qualität der Produkte wird differenziert, indem ein NIO-Zähler angeschlossen oder der Ausschuss händisch eingegeben wird.
Über den Webbrowser erhalten Sie Zugriff auf das Gerät und Transparenz in der Produktion. Sollte eine Netzwerkanbindung nicht realisierbar sein, ist auch der Offline-Betrieb möglich. Die erfassten Daten werden in Live-Ansichten dargestellt und können komfortabel ausgewertet werden.
Viele unserer Kunden haben vor der Einführung des MES FASTEC 4 PRO die Potenziale in ihrer Produktion mit easyOEE identifiziert.
Belal Al-Shaibani, ehemaliger Prozessmanager, MEDICE Arzneimittel Pütter GmbH & Co. KG:
Wir wussten nicht, welche Verfügbarkeiten und Leistungen unsere Linien brachten. Wir starteten daher mit dem Produktivitätsmessgerät easyOEE, um eine Status-quo-Analyse an drei Maschinen in der Konfektionierung durchzuführen. Bereits im ersten Monat konnten wir dank easyOEE unseren OEE-Wert an diesen drei Maschinen um bis zu 11 % steigern. Darauf aufbauend wurde dann das MES-System FASTEC 4 PRO eingeführt, das weitere Kapazitätsreserven aufdeckte und noch einmal 10 % mehr OEE im ersten Einsatzjahr brachte.“
Marcus Bruns, Group IT Manager, Gustav Berning GmbH & Co. KG:
Die Einrichtung des easyOEE-Terminals im Vorfeld und die Installation vor Ort war in kürzester Zeit erfolgreich durchgeführt und nahezu selbsterklärend. Auch der Import der Artikelstammdaten aus dem ERP-System war problemlos möglich und schnell erfolgt, um eine parallele Stammdatenpflege zu umgehen. Durch die zusätzliche Anbindung eines einfachen Handscanners werden die Prozessdaten wie Artikelnummer und Prozessauftragsnummer vom Mitarbeiter eingelesen und so Eingabefehler verhindert. Alles in allem eine sehr schnelle und kostengünstige Möglichkeit, um das Thema OEE im Unternehmen anzugehen und voranzutreiben.“
Christopher Fischer, Werksleitung, NaBento Vliesstoff GmbH:
Ohne größere Investitionen erst einmal die Potenziale der Produktion auszuloten und die digitale Datenerfassung an einer Anlage zu testen, war für uns die optimale Lösung. Wir wussten durch die Potenzialanalyse mit easyOEE, dass sich die Investition in eine ganzheitliche Lösung lohnt und auf Dauer wirtschaftlicher ist.“
Lösung 2: Vielfältige Lösungen die inspirieren – von der Theorie in die Praxis.
Kunde A: Kleine Ursache mit großer Wirkung – Aufdeckung eines jahrelangen Stillstandgrundes Durch das Anbringen von Kameras an den zentralen Produktionslinien lassen sich ungeplante Störungen eindeutig identifizieren. Wenn das MES eine ungeplante Unterbrechung identifiziert, ermöglicht die vollständige Videoaufzeichnung der Linienaktivität eine genaue Identifikation der Störgrundursache. Dadurch konnte bei unserem Kunden an einer Linie ein Störfaktor identifiziert werden, der seit Jahren regelmäßig Kurzstillstände und damit hohe Kosten verursachte. Eine Weiche innerhalb der Linie war minimal zu weit rechts angebracht, wodurch sich immer wieder produzierte Teile darin verhakten. Durch eine Korrektur der Weiche konnte die Störgrundursache eliminiert werden und so die Produktion der Linie nachhaltig effizienter gestaltet werden.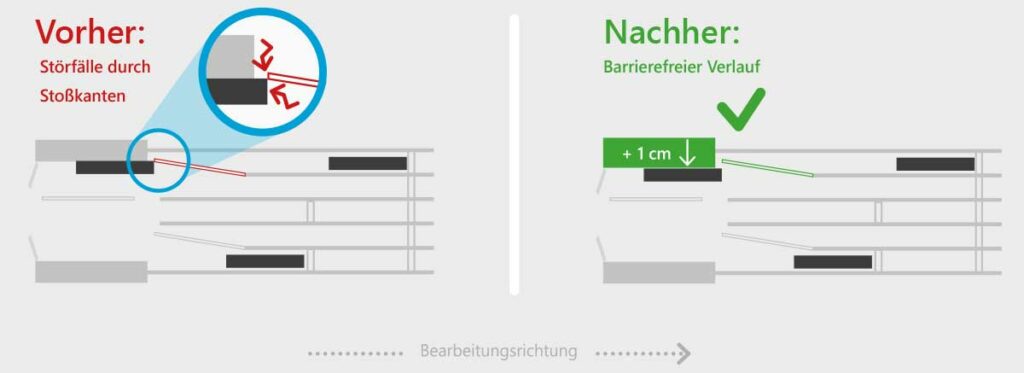
Erst die direkt an den Produktionslinien erfassten Echtzeitdaten haben die Ursache für die ungeplanten Stillstände aufgedeckt. Mit einer kleinen und einfachen Korrektur konnte diese nachhaltig behoben werden.
Kunde B: Zwei Fliegen mit einer Klappe – Kostenfreie Reparatur der Anlage und Steigerung der Produktivität
Unser Kunde fand durch digitale Datenerfassung heraus, dass die Leistungsdaten an einer Anlage nicht den Angaben des Herstellers entsprechen. Die tatsächlich in der Produktion gemessene Produktivität der Maschine wich stark von den Herstellerangaben ab. Durch die transparente, digitale Erfassung dieser Daten konnte eine Reklamation beim Hersteller vorgenommen werden. Dieser stellte fest, dass bei dem Aufbau der Anlage ein Bauteil leicht abweichend zum Optimum montiert wurde, was zu einem Produktivitätsverlust führte. Der Maschinenbauer nahm kostenfrei Optimierungen am Aufbau vor, was zum Erreichen der maximalen Taktung der Anlage und somit zu einer erheblichen Produktivitätssteigerung führte. Dadurch wurde die Produktion deutlich effizienter und Kunde B kann seither Kosten einsparen und höhere Gewinne durch gesteigerten Output erzielen.
Kunde C: Unternehmensziele einhalten – Nachhaltige Produktion und Vermeidung von Verschwendung durch Digitalisierung
Auch der Aspekt der Nachhaltigkeit kann durch transparente Daten forciert werden. Unser Kunde NORMBAU hat dazu Best Practices entwickelt. Einige ältere Maschinen wurden durch produktivere, neue Maschinen ersetzt. Mit Hilfe von FASTEC 4 PRO wird über Zähler der Stromverbrauch in kWh gemessen. Die Auswertung kann pro Auftrag, pro Maschine sowie pro Gebäude erfolgen. Durch diese Datenerfassung konnten Optimierungsmaßnahmen, wie beispielsweise die Isolierung der Heizbänder, implementiert werden. So wurden durch die Daten aus dem MES deutliche Energieeinsparungen erreicht. Für NORMBAU ist das ein großer Erfolg.
Christian Meier, Industrial Engineering, NORMBAU:
Nachhaltigkeit spielt für uns eine wichtige Rolle. Früher konnten wir den Stromverbrauch lediglich pro Gebäude bestimmen. Dank FASTEC 4 PRO sind wir heute in der Lage, den Verbrauch ebenso pro Maschine und auftragsbezogen auszuwerten. Das hilft uns dabei, gezielte Optimierungen vorzunehmen.“