User Report MEDICE
Partnering since 2011 – FASTEC 4 PRO at MEDICE Arzneimittel Pütter GmbH & Co. KG
The full report is available for download.
The FASTEC 4 PRO Software Solution at MEDICE
Since its foundation in 1949, MEDICE Arzneimittel Pütter GmbH & Co. KG has become one of the most successful family-owned pharmaceutical companies in Germany. At the headquarters in Iserlohn, more than 450 employees currently develop, produce and test high-quality pharmaceuticals and medical products.
After many positive experiences with FASTEC and easyOEE, the decision was made in 2012 to implement the MDA/PDA system FASTEC 4 PRO. Since then, the software has been continuously expanded and the Production Planning module has also been introduced. Today, the software solution is the central control element of production. Enormous optimization potentials are uncovered and gut feelings regarding machine performance are refuted in many places. You can find exciting and unexpected best practices in the user report!
- Industry: Pharmaceuticals/Cosmetics
- In Use: FASTEC 4 PRO software solution with the Machine Data Acquisition and Production Data Acquisition modules, Maintenance and Detailed Scheduling/Control Center, as well as the additional functions Monitoring, Automatic Report Shipping, Alerting, Mobile Client and Personnel Time Recording
- Interfaces: ERP interface (Infor) enables, for example, the import of production orders
c"Many manual work steps are no longer necessary. Our production planning is paperless, which saves time and is much more accurate. It is always clear which process steps we are losing time on and how well the individual orders are going."
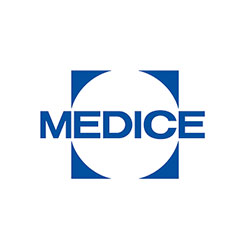
"Thanks to easyOEE, we were already able to increase our OEE value on the three test machines by up to 11% in the first month."
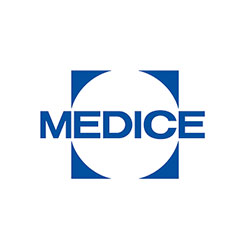
“We had already had good experiences with easyOEE and FASTEC. It was therefore consistent to also implement the MDA/PDA system from FASTEC. Especially since the modular structure of the FASTEC 4 PRO software allowed us to gradually integrate the individual areas of our production.”
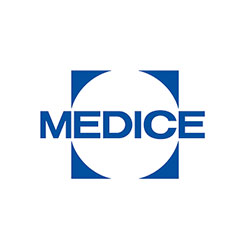
“It has an absolute added value to have your processes automatically recorded! For us, FASTEC 4 PRO is a tool to help us identify which problems we need to address in production in order to achieve gains in efficiency.”
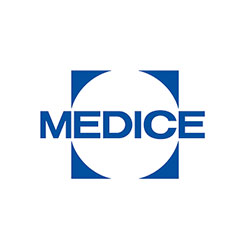
“For us, transparency led to further reductions in downtime and to a high level of acceptance of the system among our employees. Everyone takes a look at the big screen to see how production is currently going.”
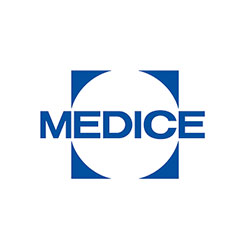
Short And Precise
How It All Started
At the beginning of 2011, a potential analysis was carried out with easyOEE in the packaging department. Based on the database created with easyOEE and the potentials identified, the decision was made to implement the FASTEC 4 PRO software. With its help, the entire production was to be monitored, controlled and optimized step by step in order to utilize the discovered capacity reserves. Thanks to transparent data acquisition, reports and the implementation of optimization measures, MEDICE was able to increase the OEE (Overall Equipment Effectiveness) by 10% in the packaging process alone. Step by step, further machines were connected, capacity reserves uncovered and optimization measures initiated.
Digital Production with FASTEC 4 PRO Today – Detailed Scheduling
Manual, paper-based production planning has been replaced by digital detailed scheduling with FASTEC 4 PRO. In the past, it was difficult to react to process modifications caused by disruptions or longer setup times, which led to inefficient production processes and, as a result, to high costs and waste of resources. Today, planning is based on the next one to two weeks, and it is also possible to flexibly adjust line occupancy in real-time in the event of short-term changes. Planners can access orders in the software and rearrange them. Without paper chaos and without much effort. The changes are then immediately and transparently visible at all terminals.
Facts Instead of Gut Feeling – Best Practices and Examples of How Gut Feeling Can Be Deceptive
For product A, the line was stopped for an average of eight hours per order due to various malfunctions that could not be defined in more detail using the available button selection. The employees assumed, based on their gut feeling, that they knew the most common cause of the malfunction. To check this, a button with the employees’ suspected cause of the malfunction was implemented in FASTEC 4 PRO. In the further course of events, it became clear that this button was hardly ever pressed and that the gut feeling was deceptive. Incorrect assessments can result in high costs for the replacement of components without eliminating the source of the error. Thanks to FASTEC 4 PRO and the detailed analysis of the cause of the fault, it is now possible to see where the problems in the production process lie on the basis of facts.

Do You Have Special Requirements for Digital Production Management?
No problem. We deliver customized solutions. With us, you benefit from extensive project experience in digital manufacturing in various industries. With over 400 customers. Worldwide. Since 1995.
Who We Work For
From automotive suppliers to food producers, pharmaceutical companies to toy manufacturers, from highly specialized niche suppliers to ambitious medium-sized companies to large international corporations – over 400 customers around the globe rely on Software for Production – made in Paderborn. Among them:
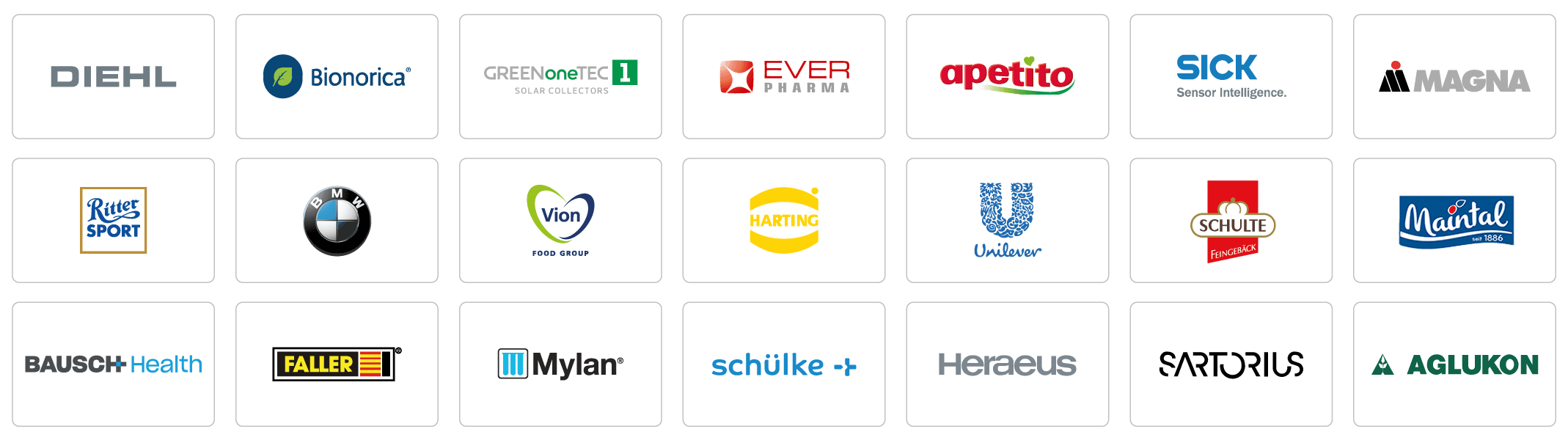
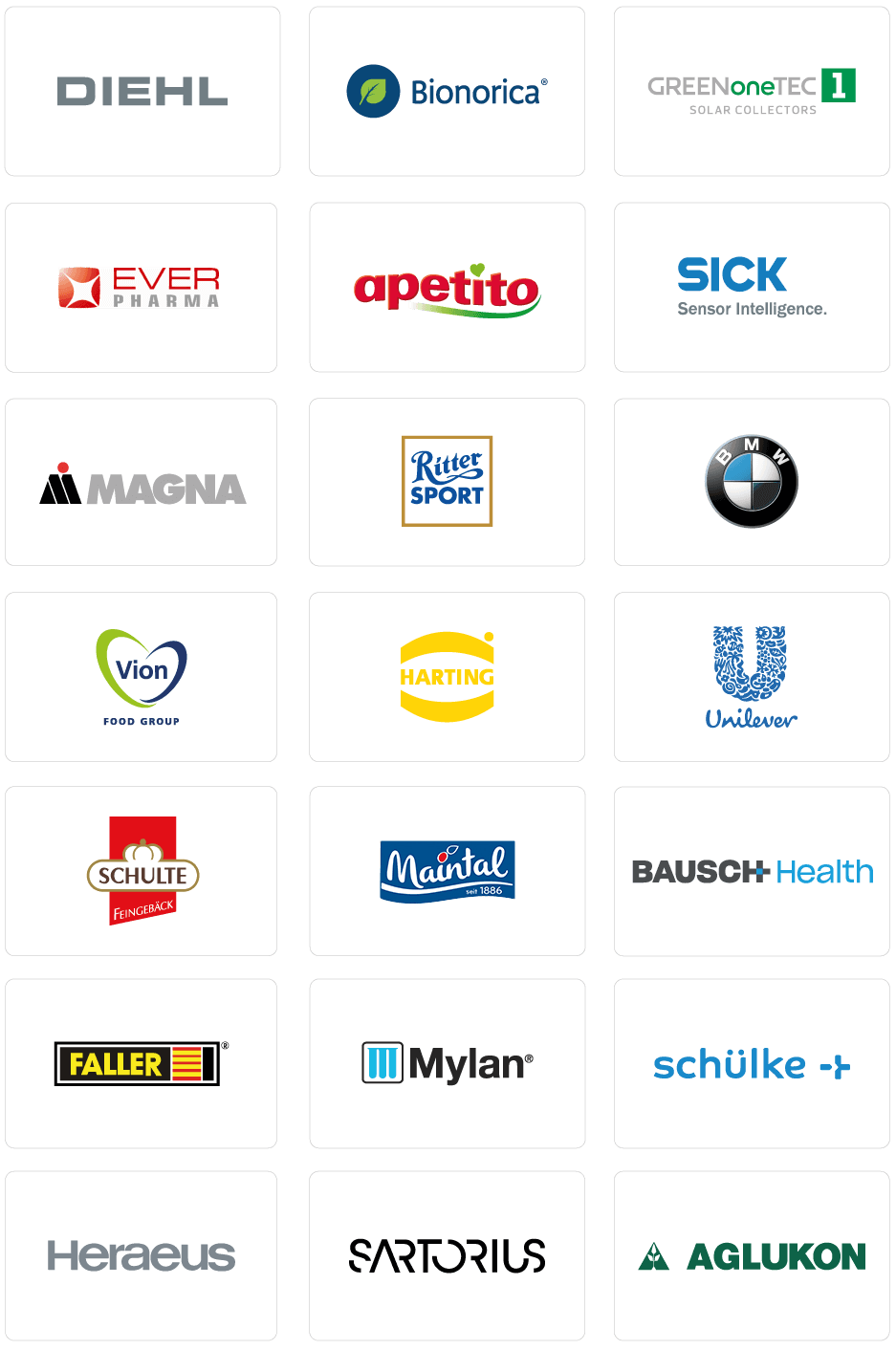