Having previously worked as a Lean Manager at the global corporation Nestlé, among others, he brought his skills to bear as Maintenance Manager at Tchibo, where he took on management responsibility in the production environment. He then worked as a Lean Manager at Schülke & Mayr GmbH in the chemical and pharmaceutical industry, where he used FASTEC 4 PRO as a tool to focus on the systematic reduction of losses on production lines.
FASTEC: Mr. Kierstein, what is the aim of Operational Excellence (OPEX) consulting?
D. Kierstein: The aim of OPEX consulting is to create added value by helping people to help themselves. In terms of operational excellence, this added value has several dimensions (performance, costs, delivery capability, safety, quality and employees) and encompasses more than just purely financial savings. The key success factors for achieving the goal are:
- A sensible set-up structure for reliable performance data and key figures. Everyday life in production companies has become too complex and fast-moving to be successful with gut decisions alone.
- A common understanding of how to interpret and influence this data and key figures.
- The use of data and key figures in day-to-day business as a starting point and for monitoring the success of improvement efforts. Ideally, tried and tested lean tools are also used here.
Without the first two factors, there is a great risk of working on the wrong “construction sites”, making the wrong investment decisions or planning production facilities inefficiently. OPEX consulting therefore relies on a holistic and highly effective approach to linking data literacy and lean.
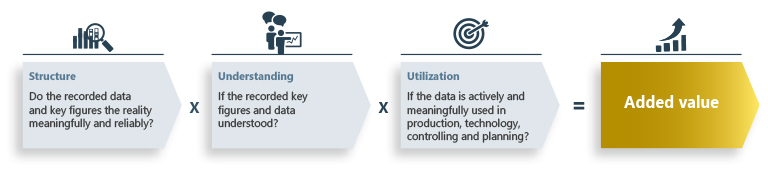
FASTEC: What initial situation do you often encounter with customers?
D. Kierstein: There are still many manufacturing companies that do not record downtimes or only do so manually. This prevents these companies from recognizing their potential and makes it all the more difficult for them to take effective measures to improve efficiency. An incorrect understanding of performance indicators can also be costly. For example, the widely used performance indicator OEE has already been “burned” in many companies due to contradictory definitions and incorrect application.
An OEE must be used in a differentiated way in order to really show the greatest potential for reducing waste. In my opinion, there is still a great need for clarification here. Based on this, only very few companies use the possibilities of live performance displays and business intelligence solutions (such as Power BI, Qlik Sense or Tableau). These tools can significantly increase the informative value of production results and thus bring more transparency to production processes. This is an important basis for a development towards operational excellence.
So if you are wondering why your investments in the form of money, time or projects are not producing the expected results, you probably do not have the transparency you need about your production results and the associated potential.
FASTEC: What added value does your support offer customers?
D. Kierstein: The right measures make production more efficient and easier to plan and evaluate financially. This usually goes hand in hand with cost savings, increased product quality, adherence to planning, higher employee motivation and improved occupational safety. After all, the common disruptive factor is deviations from the stable production process. To this end, I systematically address the points mentioned above (1. reliable data, 2. data competence and 3. lean tools) in order to improve the structure of production data acquisition and the understanding of data and key figures. This database creates a reliable basis for identifying and implementing potential for improvement.
In this way, we have already been able to achieve increases in production efficiency of 40% in my previous projects. We have also achieved great success with short-term projects (3 months). These include
- Reduction of complaints by 90%
- Reduction of center of gravity problems by 85%
- Reduction of setup times by 70 %.
In addition, a skillful balancing of competing objectives can lead to an optimal compromise that creates added value. For example, every company knows the challenges of having to achieve both production cost and inventory targets at the same time. Inventory targets (DIO, inventory range, working capital, etc.) usually have a direct influence on the size of Production orders and are therefore at odds with production costs. Ideally, this dependency should be made measurable. In this way, such conflicting objectives can be objectified very quickly in order to find an optimal compromise.
FASTEC: How do you proceed with an OPEX consultation?
D. Kierstein: Usually, the collaboration starts with a 2-3-day potential analysis. As part of this potential analysis, the organization is analysed with regard to the “7 steps to excellence” (see illustration). This is an integrative approach to developing data competence in conjunction with lean tools. Good practices as well as optimization potential and suggestions for concrete improvement measures are developed with internal experts and then summarized and prioritized. These measures can be implemented both independently and with my support.
FASTEC: Which people from the company are involved in the project?
D. Kierstein: The person who has commissioned me in the company is involved in clearly defining the objectives. My work assignments usually require cooperation between production and technology. Depending on the job, however, the involvement of Quality, Controlling and Production Planning may also be necessary. In my opinion, the principle of “turning those affected into participants” is a very good one.
FASTEC: How does the collaboration work?
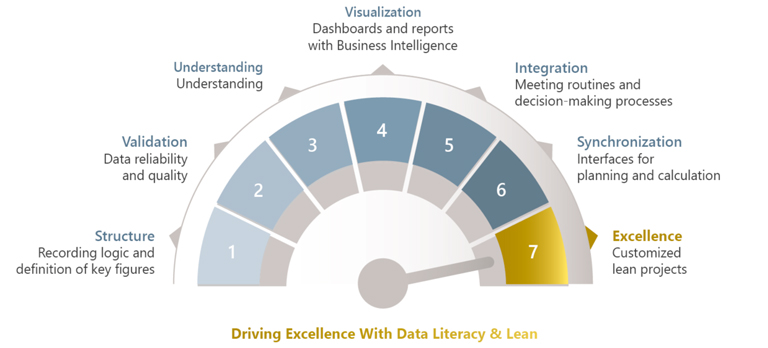
D. Kierstein: For me personally, it is very important to work together as partners and as equals. For the best possible and sustainable results, active cooperation on the part of the contact partners and an open and trusting approach are of course necessary. This facilitates the transfer of know-how and the integration of the discussed procedures into everyday life.
I generally provide support through individually planned appointments on site. Progress on projects or longer-term work assignments is tracked at least once a month. These monthly appointments can take place via online meetings, as can the majority of data analyses, for example.
FASTEC: Why is it worthwhile to seek external advice?
D. Kierstein: External consulting should close important know-how gaps in a targeted manner. I know from my own experience that, particularly in small and medium-sized companies, colleagues are responsible for a very wide range of tasks and have to function as generalists. It therefore makes sense to draw on external specialist knowledge in certain areas. In the already stressful day-to-day business, it is very difficult to acquire such specialist knowledge independently. With selective external support, quick and greater success can be achieved and costly and time-consuming errors can be avoided.
FASTEC: What methods are used for the optimization projects?
D. Kierstein: The choice of method depends on where there is a need for optimization. However, I would first like to emphasize that the first optimizations will already occur without special methods. Even the introduction of live performance displays based on meaningful key figures, for example with FASTEC 4 PRO, can already lead to considerable leaps in performance. Another example of potential that can be realized quickly and easily is the detection of unrealistically low targets for production speed (target cycle time).
In my experience, one very important method is the introduction of regular improvement routines. These improvement routines include the ongoing review of key performance indicators with the aim of actively controlling them. Ideally, such a routine is embedded in an existing regular meeting (e.g. store floor management meeting), but it can also be set up separately.
Building on this, the tried-and-tested lean tools such as DMAIC (to eliminate recurring performance losses), SMED (to reduce setup times) or 5S and Centerlining can be used and tracked in a very targeted manner.
At this point, I would like to mention again that knowledge of these methods is not a prerequisite for potential customers. In my consulting sessions, I implement individual procedures together with the users and explain everything in detail. So even newcomers who have no experience in these areas will benefit greatly.
Conclusion
Effective efficiency increases in production are achieved through the appropriate combination of data, data expertise and lean tools.
Daniel Kierstein provides support at all levels and leads your individual project to success. He is a valuable partner for us as he has many years of experience with FASTEC 4 PRO and has already gotten to know (and love 😉) our software from a customer perspective.
He is happy to share his recipes for success with you. Just get in touch with us.
Are you interested? We will be happy to put you in touch with Daniel Kierstein.
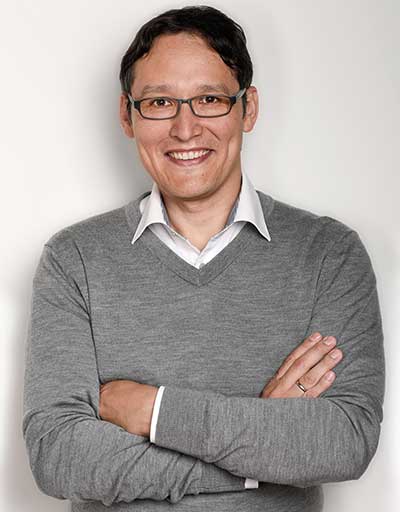
Daniel Kierstein
Independent operational excellence consultant and project manager
He has more than 15 years of experience as an implementation-oriented practitioner with a passion for operational excellence in manufacturing companies. He is familiar with the diverse challenges that arise at the interfaces between production, technology, works council, controlling, quality and logistics – not only from a purely advisory perspective, but also as an active designer and implementer.
As a certified FASTEC partner, Mr. Kierstein is at your disposal to work with you to realize the full potential of your FASTEC implementation.