The status quo is different for MES solutions: Due to the individual production processes in the respective locations, solutions were introduced in the past that were tailored precisely to the needs of the locations. In the meantime, these isolated solutions can no longer be hosted by the centralized IT department, which has led to a change in thinking.
The goal: standardized and globalized systems for all locations!
The problem: Different requirements – processes need to be adapted!
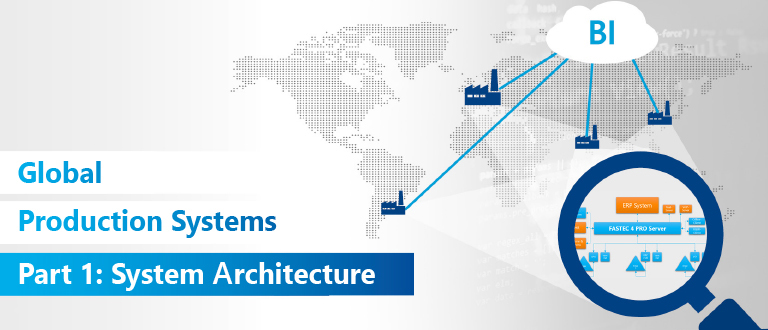
What Can a Standardized System Architecture Look Like?
Currently the simplest answer: cloud. This is also true for the future, because a centralized system can be managed well and the advantages of the cloud can be used. But what happens to the local systems that cannot simply be replaced and the servers that are still available locally?
The correct answer at the moment is: BI tool with EDA principle (EDA principle: a resource (employee, device, etc.) is “there anyway” and can be used for a new project on the side without having to purchase or hire new staff).
The local systems can continue to be operated and the data is also backed up in the cloud. There, the data can be visualized using intuitive business intelligence tools and appealing designs. This makes it possible to compare multiple locations, even with different production processes. In addition, several data sources can be tapped in order to define cross-connections.
Conclusion: The goal can be achieved with little effort without having to rethink and reintroduce all systems. Employees who work with the systems on a day-to-day basis do not have to change and global management is provided with the necessary transparency.
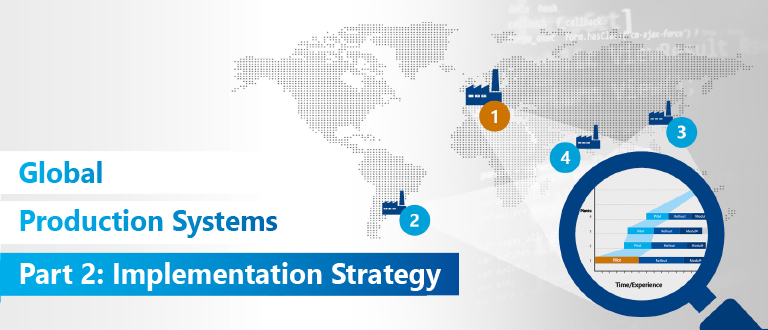
How Do You Find the Right System and How Is It Implemented?
Once a system architecture has been selected, the question now arises as to how such a structure can be set up.
The basic thesis is that the local systems are extended by a global BI tool in order to postpone the costly transition to cloud systems. This makes sense because the development of cloud systems is progressing rapidly and the status quo is not yet mature. The implementation of decentralized production systems, such as an MES, is therefore by no means outdated.
As it is a major investment decision, a selection process for the right system provider must be carried out first. This can take place internally or with external support. Goals must be defined that fit the company’s long-term vision. A specification sheet, on the basis of which the providers present their solution, is essential.
The various solutions are usually very similar, but the personal chemistry with the provider is often not. And this is precisely the crux of the matter: it is less about the possible functions and much more about the way in which we work together. The project will extend over months and years. As in a good partnership, it’s the inner values that count and not so much the appearance!
Once the right provider has been selected, the conception phase begins. This time is extremely important because it lays the foundation for later processes. Sufficient time should therefore be taken to work out the right solution. It also makes sense to put the solution in writing, e.g. in the form of a specification sheet, to ensure that all stakeholders have the same understanding.
A pilot project is then carried out, which has two objectives: Firstly, a proof-of-concept to optimize the developed concept in practice, and secondly, the development of a standard for the subsequent rollout. The pilot project should contain a large part of the core functionalities. This core will later be rolled out to all other locations. Other functions are introduced one after the other, sometimes in parallel. However, sufficient time must be allowed to ensure that change management for employees is not neglected.
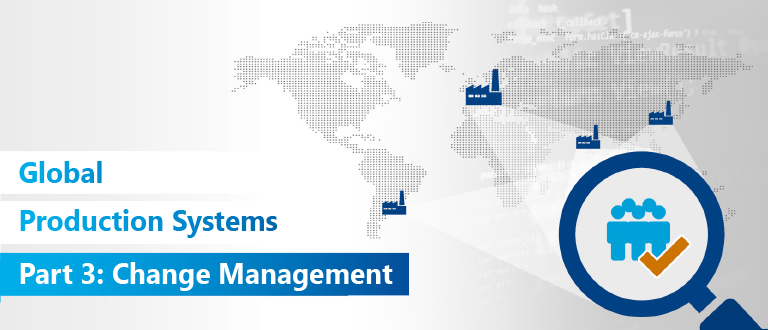
How Do You Get Employees on Board?
So far, the areas of system architecture and implementation strategy for global production systems have been highlighted. Finally, the focus is on people, who play the main role in the entire project.
When it comes to innovations, it is above all the people who have to adapt. We know from psychology that people react very differently to change depending on their character. A possible rollercoaster of emotions starts with fear, rejection and anger, for example, and ends with hope, overcoming and acceptance. Involving employees in the project and practicing the right change management is therefore a key issue for a successful project.
Project teams must be formed at both the company and the system provider, with a project manager responsible for each. All employees involved in the subsequent use of the system should be included in the company’s project team. The project manager is in turn embedded in a higher-level committee, which takes into account personnel, financial, operational and IT-related interests, among others. The interests of the employees must also be taken into account. They should contribute their ideas to the conceptual design and will thus identify with the implementation. A key user is trained for each location who will be the first point of contact for questions about the system in the long term. Responsibilities must be assigned down to the lowest organizational level in order to become efficient through the division of labor. Know-how should be distributed in the best possible way – not only through training, but also by supporting the implementation. The best strategy: teach the teacher!
Finally, when implementing global production systems, it should be noted that in addition to the right choice of system and provider, the appropriate strategy and change management must also be implemented. The interests of those involved should be taken into account. In this way, all factors that are important for a successful project are fulfilled.