Um Aufträge aus dem ERP-System auf Fertigungsebene optimal verplanen zu können, unterstützen im MES integrierte Feinplanungsmodule. Dies ist auch bei nicht optimaler Stammdatenqualität möglich.
Getting started with digitalized Production Planning is often seen as a huge hurdle that needs to be overcome before the first successes can be achieved. However, this is a misconception. Even the first, simple step of recording data digitally and in real-time shows clear success compared to Excel-based planning, for example. Faster response times allow you to react flexibly to changes, saving time and resources. It is therefore also worth starting with small steps on the path to digitalized production planning. Our new additional function “Preplanning” supports you in this. You can find out more about this at the end of the item, but for now we will focus on the planning itself.
Detailed Scheduling is when orders and operations are not just assigned to a specific shift and machine group, as is usually the case in ERP planning, but are scheduled for a specific machine and at a relatively precise time, e.g. on the basis of minutes. In the course of production control, current data from production, e.g. work progress or machine statuses, are included in the planning. The more information about the current production status that can be taken into account, the higher the probability that order planning can be implemented accordingly. At the same time, the real-time connection via an MES ensures that it is possible to react promptly to unexpected problems, e.g. machine malfunctions or a lack of resources. Planned maintenance of machines or tools, on the other hand, is automatically displayed so that the employee responsible can already take this into account in their planning. In multi-stage manufacturing or production, further benefits also arise from the fact that current material stocks such as raw materials or intermediate products can be taken into account in the planning. Unnecessary waiting times due to a lack of stock are recognized before the actual production, so that countermeasures can be taken in the planning. The potential of (partially) automated Detailed Scheduling using an MES is therefore obvious.
Planning is at the heart of production for manufacturing companies. Optimized planning and coordination of the individual processes can have immense leverage effects that greatly reduce throughput times and setup times.
Implementation of the High Planning Requirements:
Efficient planning of production and planned orders is the basis for cost-optimized and sustainable production. Delivery dates can also only be met with good planning. It must also be possible to react flexibly to changes in plans. A detailed planning module integrated into the MES helps to manage these complex requirements. It also offers the advantage that, due to its proximity to production, newly planned dates can be distributed paperlessly via terminals and a central plan is available for all to view. This is an essential information tool for sales, maintenance and quality assurance, among others. Thanks to the holistic MES integration, all stakeholders know when they can and must carry out their activities – this ensures complete transparency at all levels.
Production Planning with static setup times, as is still often the case in practice, can distort the overall plan and make it inefficient. Depending on the previous occupancy of the line and optimized sequence planning for production orders, setup times are dynamic. Cleaning and contamination matrices are crucial for deriving setup matrices and thus more accurate setup times.
With the Detailed Scheduling module in MES FASTEC 4 PRO, you also have the option of defining individual set-up rules. In contrast to extensive matrices, the effort required for a broader product range is significantly reduced and hardly any subsequent maintenance is necessary.
Semi-automated planning in the MES gives your planners the flexibility they need to act individually and reliably – and takes the pressure off their day-to-day decision-making processes!
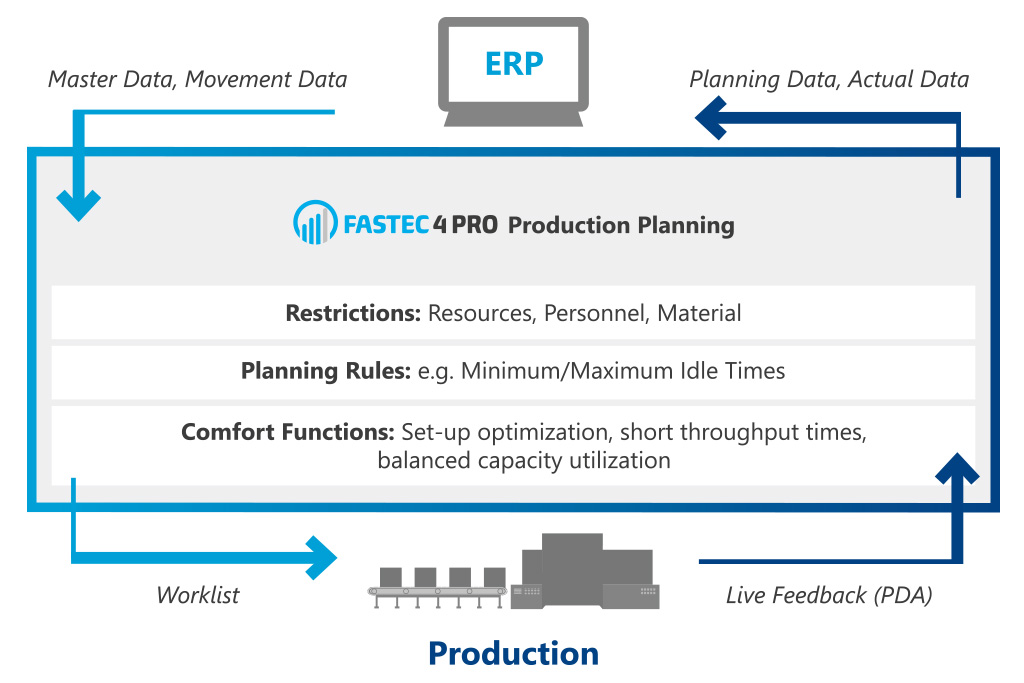
Functionality of the FASTEC 4 PRO Module “Detailed Scheduling/Control Center” | Graphic: FASTEC GmbH
The MES module “Detailed Scheduling/Control Center” consists of several tools that save a lot of time compared to planning methods with spreadsheets or planning boards. Examples:
- Reports and dashboards that provide information on the current status of production and facilitate readjustment in the event of deviations from the plan
- Gantt plan displays that incorporate current production data and machine statuses in real-time, provided you also use the MES Machine Data Acquisition module
- Ergonomic and user-friendly operation, e.g. by simply moving orders in the Gantt chart using drag & drop
- Immediate visualization of the effects of changed planning on other orders
- Waiting and idle times between operations and production planning are taken into account in the production plan
- Automatic consideration of required capacities for processing the work steps
- Consideration of alternative operations or work plans including necessary transport and idle times
- Optional scheduling of production order networks
- Check for individually definable rule violations, e.g. sequences, deadlines, capacities
- Alternative planning scenarios for comparing different strategies
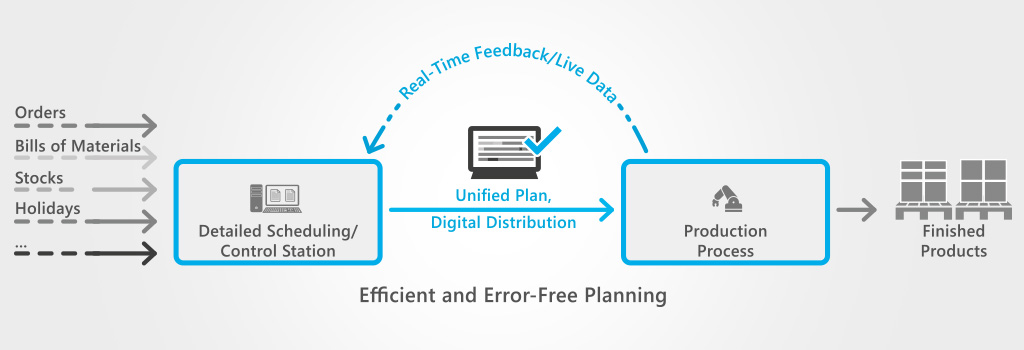
Convenient and Effective Planning with our FASTEC 4 PRO Module “Detailed Scheduling/Control Center” | Graphic: FASTEC GmbH
A frequent problem in detailed scheduling projects: Insufficient master data quality
In order to be able to optimally plan orders from the ERP in the MES, a high level of master data quality is required. However, this is precisely where many companies fail, especially SMEs, some of which have grown over decades – and with them their data volumes and data structures. It is therefore not surprising that, regardless of the IT systems used, the master data quality of many companies has shortcomings. Deficiencies, for example, with regard to the structure and content of master data or the standards to be applied.
When we talk about optimizing production or increasing efficiency through optimized planning, we usually mean optimizing throughput times. The customer’s requirement is usually to obtain optimum Production Planning at the touch of a button, but this requires high-quality master data – regardless of whether the planning is to be manual, semi-automated or automated. Master data in ERP systems is sometimes inadequate and incomplete, and there are many production orders with no obvious identifiers containing products and items with different properties.
Companies are therefore faced with the major challenge of having to convert the master data to a format that can be read and interpreted by the MES before implementing detailed planning software.
Grouping and sorting is almost only possible thanks to the expertise of the planners in the company, so they need appropriate support with this activity in order to be able to work efficiently. For many companies, this is almost impossible to manage, which is already slowing them down (in the starting blocks) on the path to digital transformation. This is why FASTEC has developed the autonomous additional function “Preplanning”, which addresses precisely this hurdle and can be licensed by our customers if required.
Simple Solution: Optimize Your Database by Increasing Data Quality!
Our autonomous “Preplanning” additional function is the ideal tool for increasing data quality if the master data is not of sufficient quality. The MES additional function helps to sort and group data for autonomous planning – without having to expand or adapt the data in the ERP system. In order to be used as flexibly as possible, the additional function can be configured individually. Article characteristics such as odors, colors or packaging units can already be applied during preplanning.
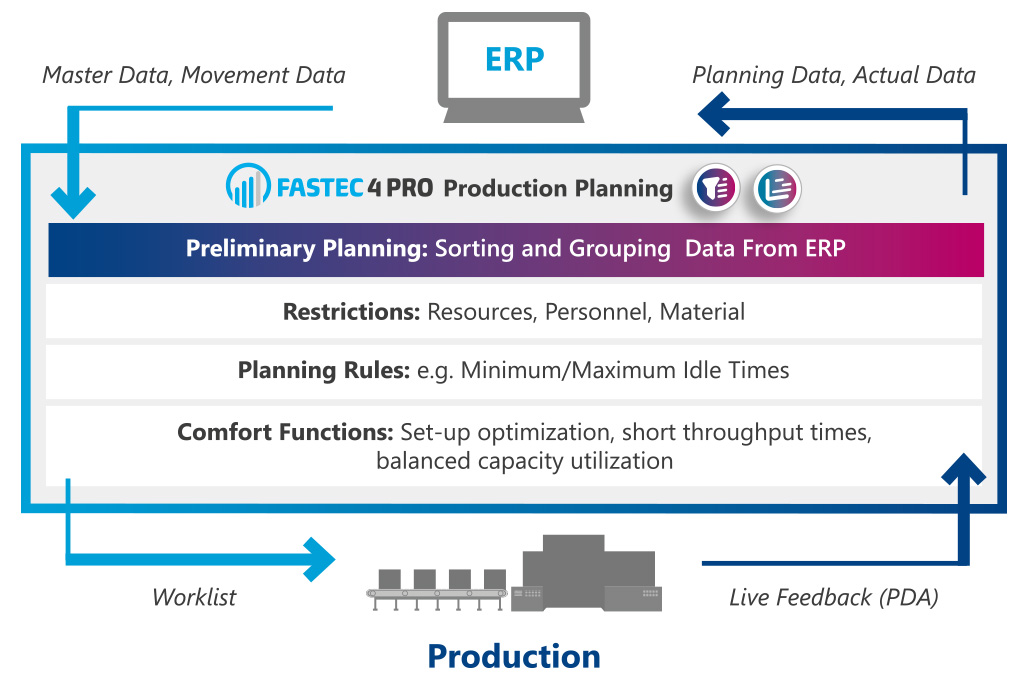
Functionality of the FASTEC 4 PRO additional function “Preplanning” in interaction with the module “Detailed Scheduling/Control Center” | Graphic: FASTEC GmbH
By supporting planners in the preparation of master and transaction data, sequence-optimized planning can already take place before detailed scheduling is carried out. This gives you a quick and uncomplicated start to your planning project without having to worry about missing or poorly maintained master data. This preparation of master data alone is the first, simple step towards optimized, digital production planning. Production orders can be combined into planning groups. These planning groups are already ideal in themselves and optimized according to production time. These planning groups can be scheduled in different places. Optimization and an overview of the related operations are always guaranteed.
The various framework conditions in the production planning process usually follow a sensible logic and therefore cannot be changed. This includes, for example, first producing light and then dark products, first producing allergen-free food before products that do not contain allergens or producing a batch completely on one machine. This is particularly important in bulk production. Cleaning times or the compatibility of consecutive items are particularly relevant here.
Preplanning is used to optimize the sequence for a specific time sequence based on definable article characteristics. Set-up times are also reduced through the coordinated use of resources, which can be planned over the entire production process. The “Preplanning” function allows the first successes to be achieved even before the minute-by-minute detailed scheduling of production.
Conclusion:
The Detailed Scheduling module and the optional additional function Preplanning provide companies with a tool for getting straight into (partially) automated planning. This tool significantly reduces the workload for planners. This opens up time resources to further optimize processes and ensure quality. In addition, efficient planning makes it easier to meet delivery deadlines, enables sequence-optimized production and helps companies to avoid waste and reduce costs. All of these benefits increase competitiveness, promote sustainable production and strengthen the company’s resilience. The company positions itself for the future.