With clear KPIs, visible processes, and daily dialogue, Shopfloor Management ensures that operations run smoothly, deviations are detected early, and everyone knows what needs to be done. It creates transparency and strengthens accountability.
This article covers:
What Is Shopfloor Management?
Shopfloor Management is the direct control and management of production processes at the place where value is created – the shopfloor. It is a key element of modern production control. The goal is to optimize production processes through transparency, a focus on KPIs, and communication. Shopfloor Management combines operational excellence with active employee involvement and continuous improvement.
At its core, it’s about making production visible and controllable. Central KPIs such as OEE (Overall Equipment Effectiveness), cycle time, scrap rate, availability, and changeover time take center stage. Through daily meetings, visual management, and active leadership, problems are identified and resolved more quickly – a crucial step toward increasing productivity.
Shopfloor Management stands for a leadership philosophy based on visibility, structured communication, and key performance indicators. With its focus on direct communication and fast problem-solving on site, Shopfloor Management is an effective tool for improving efficiency and reducing scrap.
A Manufacturing Execution System (MES) is the digital foundation for successful Shopfloor Management. It provides machine data (MDA), production data (PDA), quality information, maintenance data, supports planning, and ensures seamless traceability.
Every step in the production process is documented and made traceable. This creates transparency, reliability, and a solid basis for decision-making – live and data-driven. With an MES, shopfloor operations are managed based on facts.
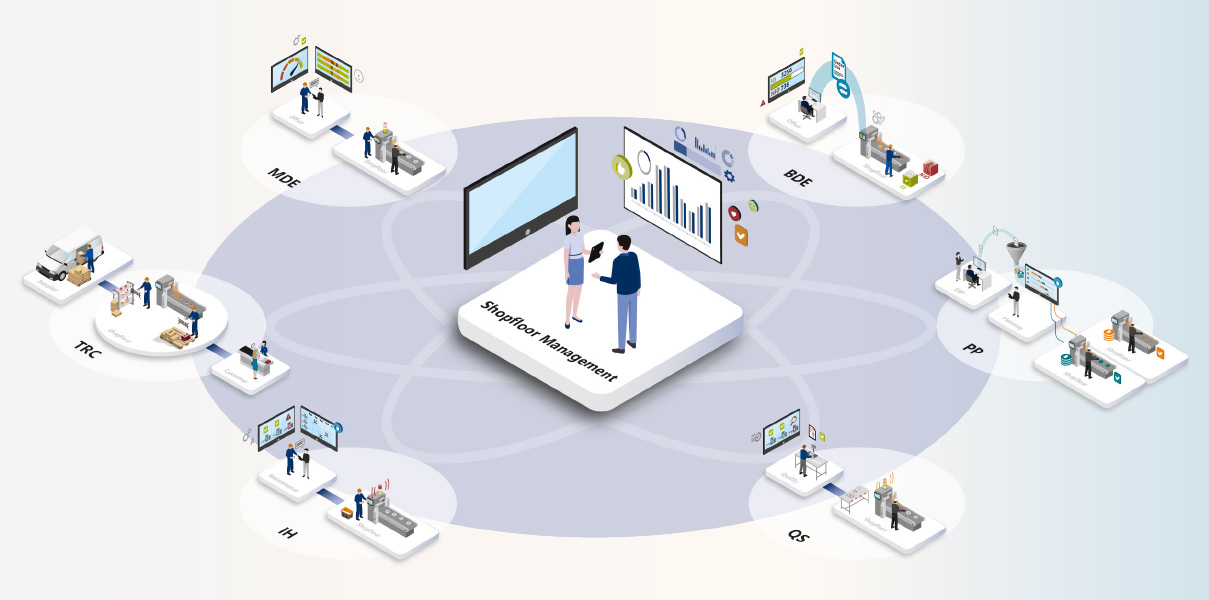
How Does Shopfloor Management Work?
Shopfloor Management works through targeted leadership at the place where value is created – directly in production. Managers are regularly present on the shopfloor, analyze KPIs such as OEE (Overall Equipment Effectiveness) , and discuss them daily with their teams. OEE is a key figure used to evaluate the productivity of a machine, system, or line. This allows all equipment losses – and thus potential for improvement – to be systematically identified, analyzed, and eliminated. The OEE value results from the product of availability, performance, and quality.
The industry portal “Industrie Wegweiser” describes that, in addition to the improvement process, Shopfloor Management consists of four key elements: leadership, communication, visualization, and structured problem-solving. Alongside strong leadership, effective communication is essential for successful Shopfloor Management – and it should take place at eye level, directly on the shopfloor. Visualization means that all involved employees have a clear overview of production by seeing displayed KPIs. Structured problem-solving involves introducing sustainable methods tailored to employees.
Why Is Shopfloor Management Important?
Leading from behind a desk quickly reaches its limits in complex production environments. Shopfloor Management, on the other hand, creates the necessary proximity to the process. It ensures that decisions are made based on real-time data and directly at the source. Communication is simplified, responsibilities are clarified, and improvements can be implemented systematically.
Especially in times of Lean Management, Industrie 4.0 , and global competitive pressure, Shopfloor Management is a key tool for managing production efficiently and continuously developing it further.
The key elements of Shopfloor Management:
- Visual management: KPIs are made visible at the point of origin. This includes OEE, downtimes, cycle time deviations, or scrap.
- Structured communication: Short daily meetings directly on the shopfloor create clarity, set priorities, and promote teamwork.
- On-site leadership: Managers are present, observe processes, talk to employees, and enforce standards.
- Problem-solving skills: Deviations are not ignored but analyzed together and resolved systematically.
- KPI orientation: Decisions are based on real-time data. The goal is continuous performance improvement.
- Responsibility: Everyone knows their tasks and goals and can understand their contribution to the company’s success.
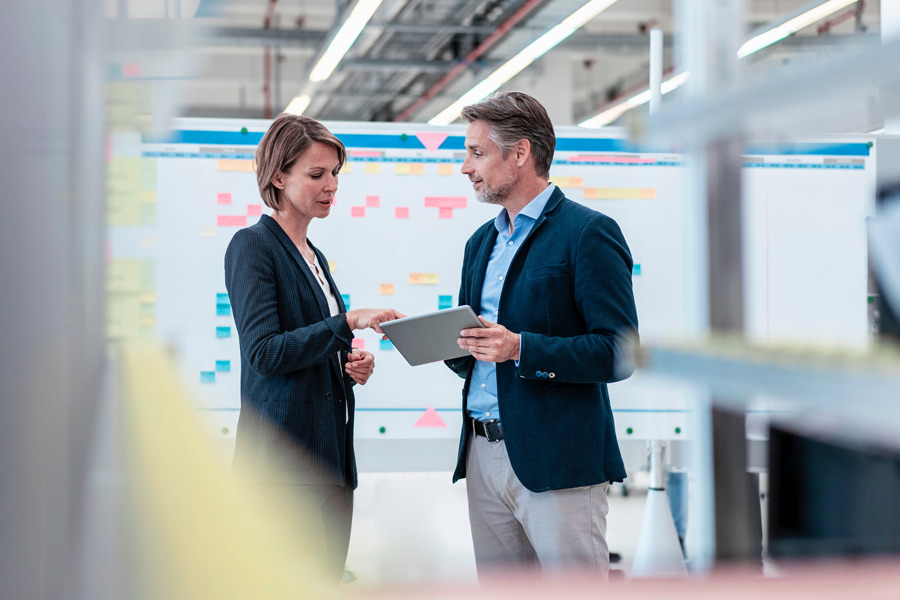
What Are the Benefits of Shopfloor Management?
Shopfloor Management offers a range of benefits for production. Here are the key advantages:
- Increased production performance: OEE values improve measurably when downtimes, losses, and disruptions are specifically addressed.
- Reduced lead time: Faster changeovers and fewer delays shorten overall production time.
- Lower scrap rate: Employees detect quality issues earlier and resolve them.
- Stronger team spirit: Involvement promotes motivation and personal responsibility.
- Reduced costs: Companies identify potential and put it into action.
- Greater transparency: Everyone involved has a clear overview of production.
When Should You Implement Shopfloor Management?
Shopfloor Management is suitable for all manufacturing companies. It is especially useful in production environments with complex processes, many interfaces, and high quality standards. Shopfloor Management supports companies that want not only to control their production but to actively develop it further. It also helps if you aim to:
- Implement lean production
- Actively manage KPIs like OEE
- Modernize your leadership culture
- Improve communication
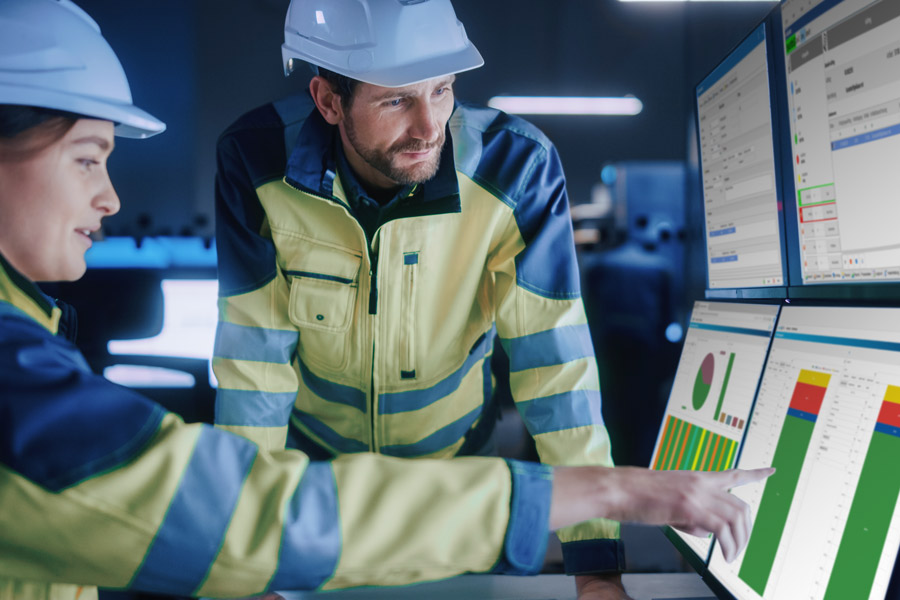
Successfully Implementing Shopfloor Management
For the successful implementation of Shopfloor Management, several points should be considered in advance. Implementation is done step by step:
- Set goals: What should Shopfloor Management achieve? (e.g., improve OEE, reduce scrap, increase transparency)
- Select a pilot area: Start small, gather experience, and continuously adapt to needs
- Define KPIs: What is measured, and how? (e.g., OEE)
- Introduce visualization: KPI boards, dashboards, etc.
- Conduct training: Prepare managers and teams for new tasks and the use of Shopfloor Management
- Establish a meeting culture: Regular, brief, and structured
- Clarify roles: Define responsibilities and strengthen motivation
- Continuously improve: Measure, adjust, and learn from experience
Digital tools such as an MES or shopfloor apps make it easier to implement Shopfloor Management. Data can be captured live and used directly in meetings. This allows changeover times, cycle times, or scrap rates to be analyzed in real time.
How Does an MES Support Shopfloor Management?
An MES (Manufacturing Execution System) is the digital backbone of successful Shopfloor Management. It provides all relevant production data in real time – from cycle time and changeover time to scrap rate. An MES like FASTEC 4 PRO handles tasks related to data collection. It enables companies to digitally collect machine and operational data for the purpose of optimizing production.This includes information on lead times, machine statuses, reasons for downtime, and duration.
The analysis of this data reveals potential sources of error in the production process and allows disruptions to be detected in real time, while also enabling targeted long-term improvements. What was once recorded manually on paper or in Excel spreadsheets can now be captured automatically – saving time for employees and increasing transparency throughout the company. An MES is also suitable for short-term evaluations and is primarily used in day-to-day operations.
In many companies, Shopfloor Management is becoming increasingly important – optimization measures are digitally organized based on production data. The improvements achieved are traceable and linked to their root causes. This provides a solid basis for justifying investments.
Jonas Drees, Head of Sales & Marketing at FASTEC
Precise Planning and Control of Production Processes
The goal of using an MES is to optimize production processes and improve manufacturing efficiency. By capturing and analyzing data in real time, MES software enables precise planning and control of production processes. Integration with other systems such as Enterprise Resource Planning (ERP) helps improve responsiveness to changes in production.
By collecting process and production data as well as material and energy consumption, companies can detect process disruptions and deviations from target values in real time. This enables early intervention. The collected data can be evaluated by order, product, or at the batch number level.
Improved Shopfloor Communication
An MES makes processes transparent. It replaces gut feeling with hard facts. Instead of maintaining lists manually, OEE values, machine statuses, or order progress are available automatically. This saves time, reduces errors, and creates clarity. As a result, daily shopfloor communication becomes more precise, focused, and measurably more effective.
An MES also enables seamless traceability. Whether in complaint management or quality assurance, an MES provides the necessary information immediately. It connects the shopfloor with the management level and enables data-driven decisions. Managers and employees can see at a glance where things are running smoothly and where there are issues. This allows them to react immediately, control processes in a targeted way, and optimize production.
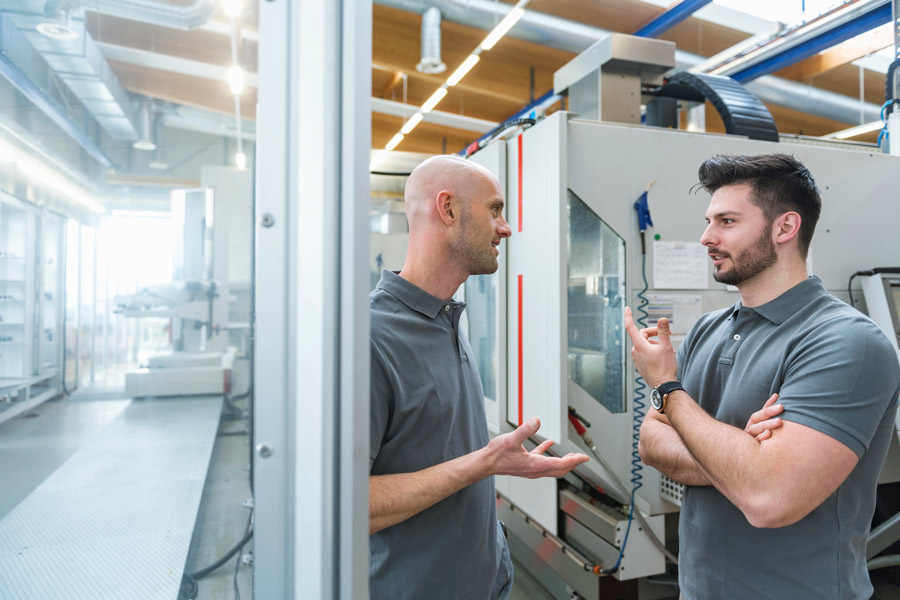
Shopfloor Management in Practice
By using an MES, employees have all the data they need to successfully carry out Shopfloor Management. The production team meets daily for coordination in a Gemba area. Gemba is a term from Lean Management and Kaizen, used to emphasize the importance of observing processes on site and identifying improvement potential.
This area is equipped, among other things, with an Andon board displaying relevant production KPIs. The goal of these meetings is for employees to engage with the data and understand its meaning – even though it is recorded digitally, the production team can still validate the numbers. At the end of the meeting, they define improvement measures.
During shift changes, it is especially challenging to transfer information from the early shift to the late shift (e.g., which disruptions occurred, which tasks are still open). This is often done verbally or with a handwritten log. An MES makes this process easier, as all necessary information is available and can be displayed. The digital form used as a shift change log includes prefilled information, and employees can add comments.
Fazit: Shopfloor Management für Transparenz und Fortschritt
Shopfloor Management works through active collaboration between managers and employees. It improves communication, enables a continuous improvement process (CIP), and optimizes production. The benefits include shorter response times, sustainable problem-solving, and more efficient planning and control. Through structured meetings, transparent KPIs, and standardized processes, companies successfully implement Shopfloor Management.
To manage production effectively, you need proximity to the process, clarity through KPIs, and the courage to communicate. Shopfloor Management is therefore not just a tool, but a leadership mindset. Companies rely on transparency, personal responsibility, and systematic improvement. The results: greater production efficiency, higher employee motivation, and fewer losses.
To implement this successfully, companies need digital support. An MES increases transparency, improves OEE, reduces scrap, and boosts efficiency. It is the ideal tool for managing production effectively on the shopfloor.
Für die erfolgreiche Umsetzung benötigen Unternehmen digitale Unterstützung. Ein MES erhöht die Transparenz, verbessert die OEE, senkt den Ausschuss und steigert die Effizienz. Es ist das ideale Werkzeug, um die Produktion auf dem Shopfloor effektiv zu führen.