Nothing is left to chance in the production of active ingredients. The smallest deviations in the production process, impurities in the subsequent packaging or incorrect labeling can render the product unusable. This is why high quality standards and documentation requirements apply in the pharmaceutical industry. The FDA guidelines 21 CFR Part 211 as well as the EU GMP guidelines and GAMP 5 for the introduction of automated systems apply. The control and documentation of processes in particular are subject to strict regulations, which is why they can make the introduction of manufacturing execution systems (MES) a costly and time-consuming process.
Whether controlling processes, planned maintenance of systems or quality assurance of products – production itself offers further challenges for the industry: lines such as those used today in filling or packaging, for example, generally consist of a large number of interlinked units, which means they have an inherent potential for disruption. The high investment costs coupled with the high personnel requirements on the lines make production downtimes a major cost risk. Therefore, all measures that lead to a significant reduction in downtimes in the long term are a worthwhile investment.
How Can the Path to Optimized Digital Production Succeed Under These Conditions?
Software-supported permanent productivity monitoring and basic fault analysis of the machinery can significantly reduce downtimes and cut costs. Without interfering with the existing control systems, additionally installed light barriers provide the necessary signals. The validated processes are not affected by this. The implementation is significantly faster and comparatively inexpensive.
On average, projects carried out by us achieve productivity increases in the double-digit percentage range. Machine Data Acquisition (MDA) constantly monitors the productivity of lines and systems and records any faults that occur. It uses meaningful KPIs (such as the OEE key figure) and provides these in informative analyses. This makes Machine Data Acquisition the first step towards sustainable production optimization in many of our projects.
The FASTEC 4 PRO Detailed Scheduling/Control Center module gives you transparency at all levels. Production coordinates the dependencies between the bulk, filling and packaging departments. Throughput times can be shortened by minimizing setup times. Live data from production also allows you to react in real-time to unexpected events. This also convinces the employees, as Belal Al-Shaibani Process Manager, MEDICE Arzneimittel Pütter GmbH & Co. KG confirms.
For us, this transparency has led to further reductions in downtime and a high level of acceptance of the system among our employees.
Your Benefit:
- Transparent, high-quality data: Digital – in real-time
- Detailed planning projects to optimize production processes
- Easy-to-implement software solutions – even without complex GMP validation.
- Fast system rollout
- Prompt results combined with low investment and time expenditure
Step 1: Potential Analysis with easyOEE
To find out what optimization potential lies dormant in your production and whether further investment in software or a new machine is worthwhile, an analysis of machine productivity makes sense. With a potential analysis, you will have the necessary data and facts to hand in just under three months.

Procedure: The easyOEE is connected to a machine. Your electrician can process existing digital signals or install a light barrier. The configuration is based on your master data. The machine operator registers a production order on the device at the start of production. The machine data is then recorded automatically. easyOEE recognizes quantities and production times. As soon as there is a stoppage, the machine operator selects the reason for the malfunction from a preconfigured list. User texts can be entered to refine the reason for the fault. It is also possible to process technical faults on the machine automatically. The quality of the products can be differentiated by connecting an NOK counter or entering the scrap manually.
The web browser gives you access to the device and transparency in production. If no network connection is available, offline operation is also possible. The recorded data is displayed in live views so that you can take action as quickly as possible. All data can be conveniently reported in order to operate lean management and OpEx. The resulting optimizations already lead to an increase in productivity.
The relevance of visualized data in real-time is confirmed by Dr. Britta Bär Head of Production, Heraeus Medical GmbH:
Simply visualizing previously perceived capacities has helped us enormously. In 2016, the OEE of individual lines was increased by a total of 10-15% within one year. This not only affects processes that are already experiencing a sharp increase in production when a new product is launched, for example, but also “mature” processes in which tasks and procedures have already been carried out for a long time and are therefore routine.
Step 2: Sustainable Optimization with FASTEC 4 PRO
Based on the data from the potential analysis, you can decide step by step and in a targeted manner which modules and functions you want to start with and how you want to proceed from there. With our FASTEC 4 PRO software, you are choosing a proven solution for optimizing your entire production. The modular FASTEC 4 PRO is the IT system at store floor level and creates the link between the technically oriented processes there and the business processes at management level.
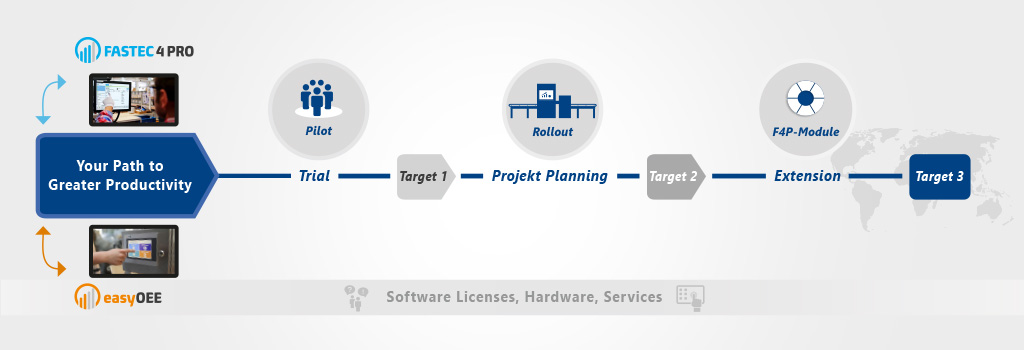
Building on the basic module, all FASTEC 4 PRO modules can be combined with each other according to your requirements. The individual modules access a common and standardized database. This means you have real-time data, there are no interfaces between the modules and therefore no duplicate data storage. Thanks to the modular structure, it is possible to implement the software modules step by step, right through to the digitization of all areas of your entire production at one or more locations.
For an easy start, FASTEC 4 PRO does not require an interface to the stored ERP. The software allows you to create and start a Production order ad-hoc using the article registration function.
Real-time data: Live monitoring across the entire line(s) allows you to see where rejects or malfunctions occur at any time – and at all levels. Once a production order has been registered, the setup times for the individual orders are automatically recorded. Interruptions are also recorded, which can then be justified manually or by machine signal. The performance recording function checks the current master data. The system’s cycles are recorded via a light sensor, for example. This makes the discrepancy between the potential technical performance of the system and the actual measured line speed visible at all times.
Intervention is possible at any time, allowing you to reduce unnecessary losses. FASTEC 4 PRO helps you to identify weak points in the value chain and derive optimization measures. This is also confirmed by the experience of our customers. Sven Katzky, EMEA Director Operation Excellence & Lean, Bausch Health:
Thanks to the FASTEC 4 PRO tool, we were able to analyze where we were losing productivity and implement appropriate improvements. This enabled us to achieve ROI within 12 months.
Your Benefit
- Fast and uncomplicated entry into digital production
- Self-sufficient system with no influence on system control and product quality
- Live monitoring: Transparent digital data in real-time, intervention is possible at any time
- Sustainable optimization of production processes
Step 3: Individual, Gradual Expansion of the Software Solution
Once the software solution has been implemented and data can be read out at the machines, further functions can be added gradually, such as the Detailed Scheduling module. The professional planning of production and planned orders is the most important basis for your optimized production. This is the only way to meet delivery deadlines, reduce throughput times, cut production costs and react flexibly to changes in plans. The FASTEC 4 PRO Detailed Scheduling/Control Center module supports your planners in mastering these complex requirements with convenient functions for efficient and error-free Production Planning. It consists of several tools that save you a lot of time compared to planning methods with spreadsheets or planning boards.
For example, frequent retooling is required for format and article changes. The FASTEC 4 PRO Detailed Scheduling/Lead Station module helps you to keep an eye on these maintenance times and plan them in a setup-optimized manner with functions such as cleaning matrices and setup rules. Production orders and batches are combined into campaigns/planning groups and the requirements of multi-stage production, with idle times during production, are taken into account. This semi-automated planning gives your planners the flexibility they need to act individually and reliably – and significantly reduces the burden on their day-to-day decision-making processes.
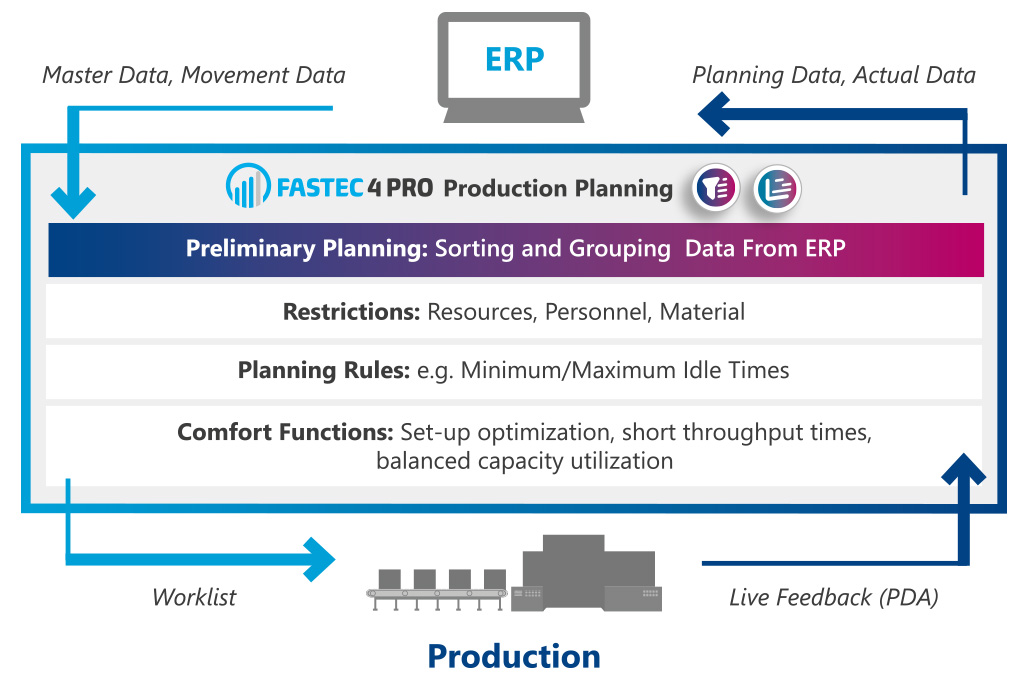
The FASTEC 4 PRO Detailed Scheduling/Control Center module also provides you with a standardized production plan that can be distributed digitally at any time. Live data from production enables you to react to unexpected events in real-time.
With our additional function “Preplanning” you can quickly and easily find the optimal data basis regardless of the existing master data quality and without having to expand/adapt the data in the ERP system
Your Benefit:
- Multi-resource planning with consideration of dependencies
- Supplementary personnel, equipment and material availability planning
- Consistent transparency across the entire planning process, recognition of bottlenecks and capacity reserves
- Standardized production planning that can be distributed digitally at any time
- Live data from production enables you to react in real-time to unexpected events
- Relief through executable and error-free production planning