For the family-owned company Rügenwalder Mühle, applying responsibility means not acting today at the expense of tomorrow and not acting here at the expense of elsewhere. Rügenwalder Mühle has therefore set itself the goal of making its food production climate-neutral by 2025. Reducing the environmental impact of emissions and conserving resources, which goes hand in hand with reducing packaging waste, are particularly important.
Sustainable Production: Why an MES is an Indispensable Tool
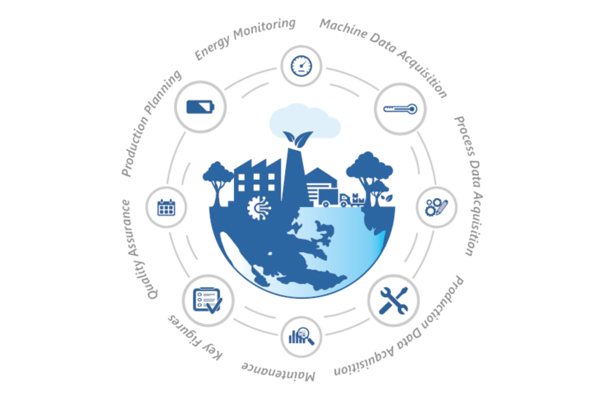
1. Transparency Across all Processes
In the past, production was “blind” in many areas of the production process, as there was no process transparency. The possible production volume was also estimated. A randomly determined number of units was produced both in the morning and in the afternoon.
2. Uncovering Potential, Implementing Optimizations
The performance of the production facilities was unknown as well. The downtimes that occurred at the plants each year were not transparent. As a result, waste due to production downtime could not be avoided, potential could not be uncovered and consequently performance could not be improved due to a lack of a basis for assessment. “Acting on gut feeling” was the daily business.
3. Making the Best Use of Resources
When demand increased, additional resources were made available in the form of equipment or staff. It was not known whether potential was still available in existing resources.
4. Avoiding Rejects and Waste
In order to conserve resources and avoid waste, evaluations of current data from production are indispensable. By analyzing this data, sources of error in the production process can be identified at an early stage and the need for action can be specifically recognized. Production management can take targeted countermeasures and completely avoid or significantly reduce rejects. As a well-known, innovative company, Rügenwalder Mühle has secured its long-term competitiveness thanks to the introduction of an MES solution.
5. Ensuring Quality
As the machine data is continuously recorded in terms of quantity and quality produced, Rügenwalder Mühle’s quality management has transparent data on compliance with defined quantity and quality parameters. This reduces material waste and ensures the high quality standard.
6. Increasing Efficiency
Digitalization makes a major contribution to increasing material efficiency – during production, packaging and through paperless manufacturing.
FASTEC 4 PRO has Become an Integral Part of Everyday Life
A few years ago, experience was already gained in digital data acquisition with easyOEE. With the construction of the new packaging plant, both plants were then equipped with the integrated software solution FASTEC 4 PRO. The OEE value is the key performance indicator at Rügenwalder Mühle and is used as a basis for assessment at all levels.
Almost all areas of the company work with data from FASTEC 4 PRO, for example packaging, production, research and development and engineering. A continuous improvement process is anchored in the corporate culture.
The aim is to increase both the productivity and the resilience of the systems. Evaluations of risks associated with increased volumes on lines are also essential. If certain lines have problems with large production volumes, production orders can be distributed differently in order to harmonize the load and increase efficiency in the long term.
Supply Planning also uses the data, for example, to provide a basis for decisions on investments in the expansion of resources.
The diverse graphical display options are very convincing. We can always assemble the views flexibly, just as we need them.
– Sergej Oks, Lean Change Agent, Rügenwalder Mühle
Result: Production is Fit for the Future
The sustainability aspect, which is deeply rooted in the company’s values, is reinforced by the digitalization of production. When systems run without malfunctions, less waste is produced and production capacities are fully utilized. This conserves resources such as packaging material and CO2 and makes production more sustainable in the long term. Waste that was previously not transparent is now specifically identified and avoided.
FASTEC 4 PRO has definitely paid for itself, as many savings as we have been able to make through fact-based decisions.– Sergej Oks, Lean Change Agent, Rügenwalder Mühle
For detailed information on the optimization projects implemented and the use of the software solution, read the entire user report.